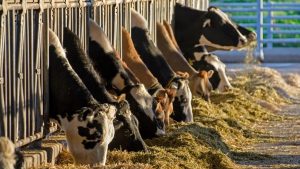
They’ve slowed down since the height of the pandemic, but social media pictures of sparse grocery store dairy displays are still popping up, and they are all the evidence needed to know that, while milk is still flowing on the farm, transportation issues are sometimes preventing milk from reaching customers.
The reasons for these issues are generally the same as the reasons everything from farm supplies to exports are moving slower these days: labor shortages (of truck drivers and even at plants) and higher costs (for labor, fuel, parts, and trucks).
Truck driver shortages were becoming a concern even before the pandemic and have now exacerbated throughout the country. Roger Nordtvedt described on the August 31 Hoard’s Dairyman DairyLivestream that Southeast Milk Inc. has had many experienced drivers retiring without much availability to replace them. Working conditions play a part in that shortage as milk haulers must run 365 days a year.
“We see a lot of young drivers coming into us for maybe 6 months to a year to get some miles under them, then they leave us to go to the cross docks that work Monday through Friday with holidays off,” said Nordtvedt, who recently retired from directing logistics and transportation for the Belleview, Fla.-based co-op. He noted driver pay has also shot up; it’s not unusual for top drivers to be making six figures. A $5,000 signing bonus, like Southeast Milk employed, looked enticing until another trucking company offered $10,000.
Unfortunately, a lack of access to trucks with drivers means sales opportunities sometimes go unfulfilled, said Corey Gillins. In his work with Dairy Farmers of America’s Mountain Area Council, they try to alleviate this by using their own trailers and looking for over-the-road haulers that only have to supply the power unit.
That approach is also used by Lone Star Milk Producers, and Jeff Sims said it has worked well for the co-op to move most of its milk with its own trailers. “It’s extremely expensive, but it gives you some more flexibility,” he said.
Another strategy that requires more investment from milk handlers but has been implemented to ease transportation challenges is drop and hook systems. This involves dropping off a full load near the processing plant and heading back out with an empty trailer without waiting for the first trailer to be unloaded. “It lets over-the-road guys do over-the-road stuff and lets short haul guys go between the drop yard and the plant,” explained Sims.
Especially in the Southeast, drop and hook has helped reduce plant detention times. Having handlers carry a bigger inventory of trailers is more expensive, and trailers still need time to be washed, but it also allows for greater flexibility to keep trucks on the road. “Our experience has been good with drop and hook as a logistical tool,” said Sims. “You almost start thinking about those drop yards as inventory management spots.”
In Gillins’ case, scheduled delivery times and slip seeding help manage inventory. They are also able to track delivery time accuracy and unloading efficiency and share that information with their plants to monitor performance.
“We feel like it’s easier today to have access to equipment than it is to have access to drivers,” he said. “So, we’re trying to utilize our drivers the most efficiently we can and utilize equipment to be what’s sitting at a plant.”