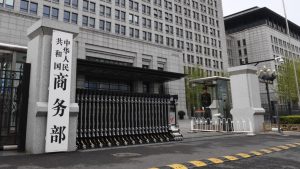
Between changes in client needs and capabilities as well as farm production fluctuations, it’s the responsibility of the milk handler to add or cut loads, often on a daily basis and typically on short notice.
“While this has always been challenging, it’s become increasingly difficult to manage over the last few years,” described Corey Gillins, whose responsibilities as chief operating officer of Dairy Farmers of America’s (DFA) Mountain Area Council include overseeing the co-op’s transportation fleet.
Trucking costs and labor shortages have affected milk hauling in recent months and years like they have nearly every other farm and life input. The lack of truck drivers was just becoming an issue prior to the pandemic and has since intensified, Gillins noted, making moving perishable milk within and between markets limiting. Additionally, costs for new milk tankers, fuel, tires, labor, and parts are all up.
Some solutions
What is being done to combat these factors and ensure milk gets to the customers that need it? Gillins outlined the strategies his team and groups around the country are using on the August 31 Hoard’s Dairyman DairyLivestream.
At the top of the list is maintaining relationships and daily communication with customers and their broader network, Gillins said. This keeps clients aware of any transportation issues that arise and allows DFA to see where milk may need to be moved to or from. “We’ve found there is some inherent balancing capacity in just working within our network,” he explained.
Another way they are able to balance milk and pivot to different customers is by using satellite transportation locations near a pocket of farms. Gillins shared an example where they have three large farms within 3 miles of each other that are 35 miles from three plants in one direction and 50 miles from two more plants in the other direction. They have begun basing trucks at the largest of these farms so milk can easily be transported in either direction based on needs.
“This approach also gives us the ability to stairstep milk to more distant markets using our own transportation when over-the-road haulers are unavailable,” Gillins added. That’s not an uncommon situation, and even though this region is using about 70% DFA-owned transportation, Gillins said contract hauler pay has increased just as they have had to raise wages for their own drivers five times in the last couple of years to stay competitive. For their drivers, they also manage schedules to reach 80% of their legal hours so that the remaining hours can be used when routes change.
To reduce the total number of trucks and tankers needed, DFA has begun using 90,000-pound trailers in Colorado and part of Idaho. “Those larger units have allowed us to reduce our equipment needs and our driver needs by about 20%,” Gillins said.
When those new trucks are added, though, others aren’t sold off, as was standard before. Instead, they are kept as mobile storage capacity to hold milk through plant issues, holidays, or even weekends and then be delivered locally as space allows. Gillins said these tankers have given them storage for 15% to 18% of daily member production.
These practices help alleviate some of the transportation issues of moving milk to markets and offer some flexibility for milk handlers and buyers. Still, it’s clear that as the processes continue to be bottlenecked and expensive, it will be a challenge to reach customers. “The lack of available transportation actually puts milk at risk of being dumped at times, leaving some available sales opportunities unfulfilled,” Gillins recognized.