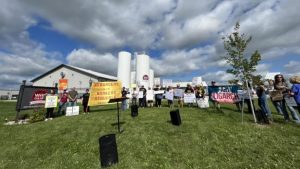
Lactalis Australia has become a favourite among Australian households over the years, with its Pauls, Zymil, Ice Break, OAK, Breaka and Vaalia dairy product lines being popular choices for many.
The business is owned and operated by Lactalis Group, the giant global business which is among the world’s largest fresh dairy companies with over 250 production sites and 80,000 employees across 94 countries, and thus it benefits from the significant multinational scale and ambition the parent company has achieved since establishing in 1933.
One of Lactalis Australia’s key commitments is providing exceptional products and services to its customers through efficient, agile and sustainable logistics, and in recent times, the key to this has been its partnership with Scully RSV.
At the end of 2022, Lactalis signed a five-year contract extension with Scully RSV on the back of a fleet renewal program the year prior for the hire of a rental trailer fleet in its three Queensland, New South Wales and Victoria operations.
As part of the contract, Scully RSV would be responsible for replacing 20 aged assets of Lactalis’ Victorian fleet with brand-new trailers built to a custom specification, which, upon deployment, would carry 3.8 million litres of flavoured milk products per week in 200 deliveries through Melbourne’s central metropolitan and Victorian regional areas.
In order to achieve this, Scully RSV worked directly with Lactalis and its preferred trailer OEM, Vawdrey, on a design that addressed a number of unique challenges in the fleet’s Victorian distribution centres and daily operations.
Two years down the track, the transition is now complete and the results have been significant. Lactalis Australia National Transport Operations Manager, Andrew Karetai, says the program has been very successful, resulting in a range of benefits – primarily reliability across the fleet.
“Getting from point A to point B and knowing that our cold chain and product integrity is being maintained is paramount to our business,” he says. “As a transport operations manager, that is my goal – to ensure that product reaches the customer in a saleable, safe, compliant manner.
“With Scully RSV, we’ve got that reliability and confidence in the fleet. The build and design of the trailers are specific to our needs in terms of strength, durability, cleanability as well as trackability.
“And at any given time, we can log in and see exactly where these trailers are, what temperature they’re running at and if there’s any issues. These are all critical components of our food safety management system that extend beyond the walls of the distribution centres and production facilities.”
The trailers, set up as B-double combinations, were spec’d with a number of unique features for Lactalis’ direct needs.
Their ThermoKing A500 refrigeration systems in the new trailers, as Andrew explains, have been a massive investment for Lactalis by providing reliable, consistent and energy-efficient cooling to protect the business’ precious freight while at the same achieving enormous reductions in fuel consumption.
“We’ve gone from using about 3.6 litres of fuel per hour down to around 1.6-1.8 litres per hour,” he says. “So, our fuel consumption is through the floor.”
Working hand-in-hand with the fridge motors, the trailers were designed with insulated roller doors which prevent the rears of the units from overheating. In this space, they also feature switches which automatically turn the fridges off when the doors are open.
The trailers have a tall aperture at the back which allows Lactalis to double-stack pallets – maximising payload and reducing the number of trips travelled annually. In the rear, electric standby power outlets were also installed to allow efficient access while in dock and limit use of diesel.
Other important features include e-track rails which provide Lactalis with flexibility in terms of load restraint options, special order load locking rails for effective restraint of loaded milk crates, strategically located work lamps on all A trailers to assist with hooking up of B trailers at night, steel and non-slip flooring inside the vehicles for easy cleaning and maintenance and rear under-run bars with increased ground clearance to prevent damage to both the trailers and loading docks at Lactalis’ major distribution centres in Victoria.
Lactalis’ attention to detail also came down to the location of the kingpins on all of the B trailers, which were moved for flexibility and to cater for the driveways at Lactalis’ sites which have extreme entry and exit angles.
In addition, Lactalis was also able to achieve significant weight reductions (as well as further contributions to greater payloads and reduced fuel usage) by specifying alloy wheels and removing features such as bar boxes and toolboxes.
“The specifics of the trailers are paramount for us making sure that we’ve got the right equipment for the task that we’re doing,” Andrew says. “Scully RSV’s ability to nurture that and make it into what we’ve got in front of us is really important. They’re definitely the special features that are helping us get through days, weeks and years of good operations.”
According to Andrew, the attention to each and every crevice of the trailers’ design has already paid off in the on-road performance of the units deployed so far.
“We saw repair and maintenance spend drop by 38-odd per cent once we got a full fleet coming on board,” he says. “We’ve been able to maximise our payload so that we can increase the weight carried per load, which has reduced the number of trips taken each week. We’ve also seen a dramatic reduction in fuel spend based on the efficiencies of the fridge motors on the trailers.”
As a result, Andrew says the trailers are paramount to Lactalis and it getting its products to the market.
“If we didn’t have a strong, reliable fleet, we wouldn’t deliver,” he says. “Our KPI is on-time delivery (OTD), and our national OTD sits at 96.3 per cent for the last month which is really strong. We’re sitting at about 99.8 per cent for our Queensland operations and NSW and Victoria are in the high 90s, based on a good, stable fleet delivering the product.
“We’re not seeing fridge failures, product temperature abuse or anything which would cause a disruption to our supply chain. So, that level of performance and consistency is paramount to us building trust within our network and with our customers, and maintaining that through having a good, solid trailer fleet.”
For Lactalis, safety is a huge priority. As Andrew puts it, whether workers are a cleaner or a truck driver, there is safety system in place to ensure they get home in the same manner that they arrive at work in. Scully RSV, in this regard, has been vital to Lactalis.
“Part of that is having the right equipment to do the task well and ensuring that the equipment we provide our people with is designed specifically for the task and has all of the right features to complete the job safely,” he says. “Our trailer fleet is exactly that. So, as a partner in that space, Scully RSV has really come on board for the journey.”

You can now read the most important #news on #eDairyNews #Whatsapp channels!!!
🇺🇸 eDairy News INGLÊS: https://whatsapp.com/channel/0029VaKsjzGDTkJyIN6hcP1K