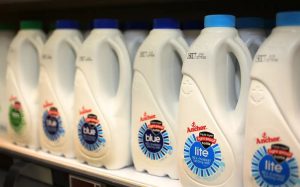
There are some producers who believe that the dealers are making a lot of money at their expense, but we can attest to the fact that this is not the case.
Even though the Milk Marketing Law requires that minimum dealer prices include a 2.5% to 3.5% rate of return (Article 7, Section 801), few are breaking even and depend on the diversity of their production to keep their businesses afloat. Everyone in the Pennsylvania dairy industry operates on a pretty slim margin.
The process that board staff, dealers and accountants go through to calculate wholesale prices takes the allowable rate of return into account, but also uses a complex array of processing and transportation costs. We hold cost replacement hearings once a year for each of the six state milk marketing areas. Following testimony by staff, milk dealers and any other interested party, the board adopts new cost replacement schedules and issues official general orders.
Since it would be impractical to collect and analyze data from all dealers in the six milk marketing areas, the first step in the process in calculating cost replacement and wholesale prices is drawing a sample of dealers from each area. Using appropriate statistical analyses and sales figures for all dealers and the drawn sample, staff determines if the two groups are statistically the same. If they are, this allows work to progress using a smaller group of dealers and involves less data collection.
Once the sample is designated as statistically the same as the population of dealers in each area, data are collected from the sample members for the analysis. It is important to note that all the figures used in the calculations are from dealers’ records that have been audited by board staff.
Costs are divided into related groupings that we call cost centers for the purpose of all calculations. We also use the phrase cost per point, with a point representing a quart equivalent. The cost centers used are: receiving, lab and field work; standardization and pasteurization; bottling; cold room; delivery; and selling.
Sub-areas of the cost centers include data about container costs, loss of fluid as it moves through the production line (shrinkage), costs of added ingredients such as flavorings and sugar, utility costs, diesel fuel allowances and labor expenses.
The price paid to producers is also figured into minimum wholesale prices that are established by the board during the cost replacement hearings. They are based on latest available published prices. Board staff make monthly adjustments to the minimum wholesale price to accommodate changing producer prices as published by USDA.
Staff calculate a wholesale price buildup for each area that is rather detailed in that it outlines separate prices for each type of milk (e.g., whole, skim, flavored) and each size of container (e.g., gallon, quart, pint). And, these prices are calculated for each of the six milk marketing areas.
It is a lot of work and there are many places along the way at which errors can occur. For that reason, multiple checks and balances are provided and the figures are also verified by accountants employed by the milk dealers’ association. By the time the board receives the testimony and exhibits containing all the relevant calculations, members can be assured that the numbers are correct. This is extremely important to all board and staff.
PMMB is always available to respond to questions and concerns. I can be reached at 717-210-8244 and by email at chardbarge@pa.gov.