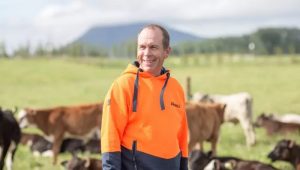
Bannister Downs early business as a niche-market white milk producer and low-temperature pasturising processor was largely built on the ability of its milk to froth better for espresso coffee than milk from mainstream processors.
Two marketing points of difference from mainstream competitors enabled the fledgling business to get a toe-hold in 2006 and grow – its unique environmentally sustainable Ecolean soft pack that stacked flat when empty and quality milk that frothed.
These made Bannister Downs a favourite with Perth’s restaurant barristers.
The Bannister Downs name gradually spread from baristas to people with coffee machines at home, and the fourth-generation dairy farm plus milk processor business has not looked back and now employs the equivalent of 50 full-time workers from the local area.
So milking unstressed cows to produce frothy milk was important, Bannister Downs’ general manager, recently retired Western Dairy director and co-host of the 20th annual WA Dairy Information Day, Mat Daubney, explained to more than 400 people who attended the event recently at Northcliffe, WS.
Presented by Western Dairy and Dairy Australia, Dairy Innovation Day 2019 was held at The Creamery, Bannister Downs recently opened-to-the-public, impressive award-winning, anodised aluminium-clad building housing its 24-stand DeLaval voluntary milking robotic rotary dairy, new low-temperature milk processing and packaging plant, cool room product storage and dispatch area.
Unique in Australia, The Creamery offers visitors the opportunity to watch every step of the Bannister Downs operation from a first-floor glass-lined viewing gallery, which proved popular with Dairy Information Day visitors.
The Creamery’s robotic rotary dairy operates with five camera-guided robots, two for udder preparation and two for cupping the robots treat front and rear quarters of the udder separately and one for teat spraying and cup washing after milking.
Milk meters monitor individual quarters, measuring flow rate, milk yield, conductivity based on salt levels in the milk and a potential early indicator of a problem like mastitis and discolouration blood in the milk may also indicate a problem and raise an alert if anything outside predetermined parameters is detected.
Cups are removed individually as flow rates diminish and if a cow stands on a suction hose or the robot cannot place a set of cups for any reason, that cow gets another ride around on the platform while only the two quarters that were not milked out first time are cupped second time around.
Cups are automatically washed inside and out between cows.
The robotic rotary dairy is supported by a 350-hectare pasture milking platform of predominantly ryegrass and Balansa clover, in part over-sown with Capello vetch for the important early biomass it produces.
Cows are also fed oaten hay in the paddocks to supplement pasture outside the growing season.
The pasture platform is divided by four laneways to the dairy the most distance cows have to walk is about 1.5 kilometres and access to paddocks is controlled by electric gates set to change at eight-hour intervals so the robotic rotary herd of up to 400 cows rotates through three paddocks in 24 hours.
Electronic NLIS (National Livestock Identification System) tags identify each cow as it leaves the paddock voluntarily to be milked.
Milking permission is determined by a combination of time since the last milking and milk yield governed by the cow’s stage of lactation.
Milking permission opens a gate to the dairy yards and access via a short lane to the rotary platform.
Cows are not fed on the platform so the dairy remains spotlessly clean, but they receive a personally tailored ration of bran and pellets, the quantity determined by milk yield and how long they have been in milk, delivered by NLIS tag recognition at a multi-stand ‘parlour’ in the exit yard before they return to a new paddock.
Via information keyed into the computer controlling and monitoring the robotic rotary dairy operation, cows requiring treatment are automatically drafted off the platform into a holding yard.
DeLaval claims the robotic rotary system has a capacity to handle 600-800 cows at a recommended 70 cows an hour, but Bannister Downs’ rotary, which has been operating since September, has already handled 90 cows an hour.
According to DeLaval’s robotics sales manager David Widdicombe, the robotic rotary was the equivalent of about eight static robotic milking stations.
The advantages of the rotary platform over a static robotic milking operation was it relied on fewer robots for the same through-put and cows tended to spend less time milling in yards and more time in paddocks eating grass, Mr Widdicombe said.
He explained that voluntarily milking cows tend to leave a paddock in small groups of “friends” and unless there were the same number of milking stations available as cows arriving, they tended to wait around in the yard for others of the group to be milked before returning to the paddock.
Bannister Down’s robotic rotary dairy and its specific pasture platform operates on a farm adjacent to the existing Bannister Downs traditional dairy operation with a 90-stand manual rotary dairy and 1000ha pasture milking platform.
This presents a unique in WA opportunity for direct comparison of operating costs and efficiencies between the two farming systems.
Of the other three robotic rotary dairies in Australia, two in Tasmania operate in parallel with traditional dairy operations, but their comparison data is unlikely to mean much in WA because of different seasonal conditions.
Bannister Downs managing director Sue Daubney said the direct comparison information from both operations was “one of the first things we want to look at” as soon as The Creamery operation was bedded down.
“But unfortunately, we haven’t had a ‘normal’ month since we opened (The Creamery),” Ms Daubney said.
The 400 cows for the robotic rotary operation came out of Bannister Downs’ milking herd of 1500 already used to a traditional rotary dairy.
Mr Daubney, who runs the farming operations, admitted there was some “pushing and shoving” to get cows onto the robotic rotary a second time after their first ride and realising there was no food until afterwards.
But they quickly adapted, he said.
“They’re happy to walk to the dairy voluntarily and be milked because they recognise it (ration afterwards) is reward for effort,” Mr Daubney said.
“(Voluntary milking) probably puts more emphasis on pasture management.
“If you allocate them too much (feed area) in the paddock then they are reluctant to leave to come up and be milked we’ve had to do a sweep of the paddock some times to get the last ones up.
“If they meet you at the gate (into the next paddock after eight hours) then you haven’t allocated them enough in the paddock they were in they know when the gates are due to change.
“That’s the real challenge, getting the balance right so they will fill up in the paddock and travel voluntarily (to be milked).”
Mr Daubney said he first considered moving to a robotic dairy about 10 years ago but was not convinced for about five years until the family started to develop plans for The Creamery and realised future expansion would require commensurate improvements in productivity if they were to succeed.
“It’s (robotics) not about getting rid of the people (needed to milk cows) but using their time more productively,” he said.
“For the past 24 years I’ve milked cows, if I had a cow that needed treatment or calves to feed, it had to be done after milking, taking my time away from other jobs around the farm.
“Now, I can do those things while I am milking because I don’t physically have to be there all the time putting cups on.
“I didn’t (previously) see the benefit for the workers.”
Bannister Downs employs about 10 full-time-equivalent permanent staff who rotate through the traditional dairy where they are washing udders and putting cups on and the robotic rotary dairy where one person can easily oversee its operation plus do other chores.
Dairy Information Day attendees also heard from Wally and Julie Bettink who farm Westland Acres at Northcliffe and many took an opportunity to inspect the Bettink’s 50-bail DeLaval rotary dairy platform and a three-pond effluent treatment system in the afternoon.
Mr Bettink said he inspected a number of operating rotary dairies on South West farms before deciding on some significant changes to the one he had built.
These changes included a platform that drains to the outside and a drain around the outer base of the rotating platform to carry water and effluent away to the treatment ponds rotary dairy platforms usually drain to the centre where wiring for electric motors and other electronic equipment like milk meters is also located.
The Bettinks’ dairy uses the same milk=monitoring system as Bannister Downs’ new dairy but without robots, which would have added “only” about an extra $50,000 to the cost, Mr Bettink said.
He said he built his original herringbone dairy himself at age 19 and upgraded it in 2010, but milking 380 cows in it was taking four-and-a-half hours, twice a day.
The only location flat enough to build a new dairy luckily was in the centre of the farm and on top of a hill which helped with drainage to the effluent ponds, he said.
Mr Bettink said water from the third pond was pumped back up and used through Yardblaster hydrants for wash down, saving an estimated 50,000 litres of water a day.
It was also used to spray irrigate a nearby paddock and he is considering trying it through a 32ha centre pivot.
The new dairy, completed last June, took five months to build using local contractors and his herd easily transitioned from herringbone to rotary, Mr Bettink said.
“Everyone told us it would take three days to train the cows and three months to train the humans, and it has,” he said.
The calmness of the Bettink herd and the efficiency of the dairy was proved at the innovation day when more than 100 visitors packed into the shed around the rotary platform to shelter from a rain squall as three workers continued milking and cows kept stepping on and stepping off without raising a tail.