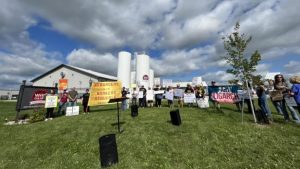
Heat stress is a prevalent issue in dairy farming that can greatly impact not just animal welfare but also milk yield. In light of the current challenges facing the agricultural sector, the gravity of such an issue is magnified. Inflation in the industry reached 30% in April, according to consultant Andersons, leaving farmers with tighter profit margins that will undoubtedly rely on production levels being kept at maximum capacity.
The heat is on
As livestock sheds are often warmer than external surroundings, cows can quite easily enter heat stress even on relatively mild days. To measure heat stress, it’s a combination of both temperature and humidity – known as the temperature and humidity index (THI). It is vital to maintain an accurate indication of THI levels as cows can begin exhibiting non-visible effects of heat stress at temperatures as low as 14°C (THI57).
Once a cow goes into heat stress, its feed intake will decline, which in turn will affect the amount of milk it produces. Furthermore, it can take up to six months before previous levels of yield are recovered. For farmers, there is the risk of considerable loss in profitability and milk production exacerbated by the long-lasting effect.
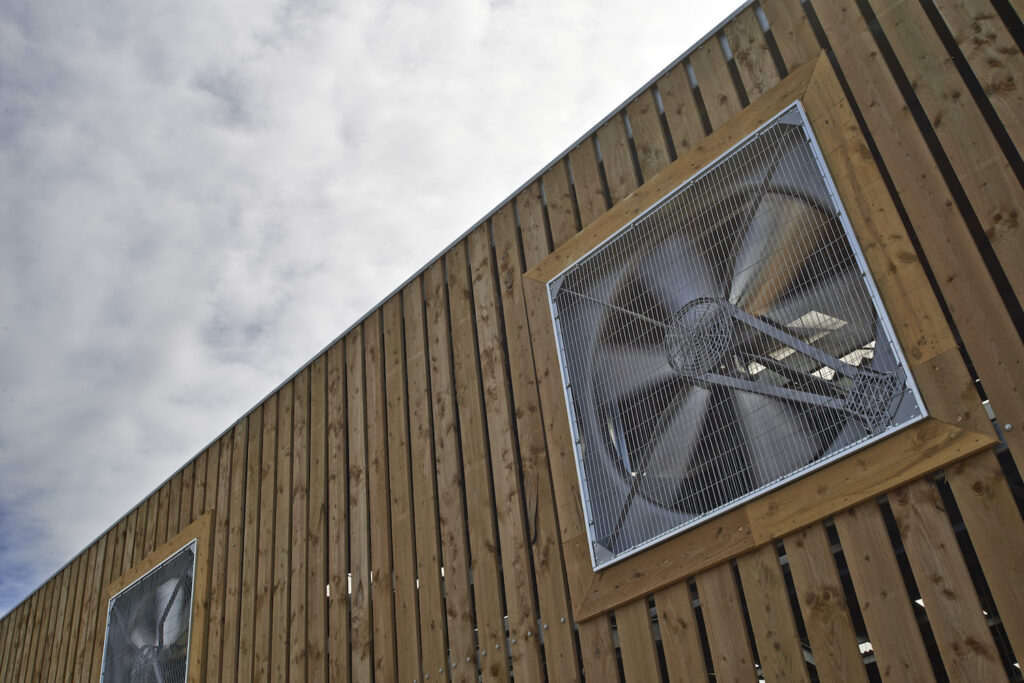
Stress relief
It is for this reason that sheds should be adequately ventilated with fans to keep cows cool. Doing so can improve animal welfare due to the reduced risk of respiratory diseases, and at the same time ensure better milk yield.
Certain supermarkets are also incentivising farmers with more money per litre of milk if farmers can demonstrate that they are looking after their animals to certain standards. Given the inflationary climate, it is imperative that the industry makes the most of such schemes.
With the aforementioned in mind, dairy farms should be ensuring that their ventilation systems are in good working order and consistently maintain them for optimum performance. Not only does this mean that livestock benefit from cooling, but it is also more energy efficient for the site if fans are operating at peak performance.
Sustaining systems
For ventilation systems like Hydor’s HV fans, maintenance is usually a simple case of managing belt change and tensioning, which can be performed by farmers themselves. The process involves first isolating the fan, removing the guards off the unit and inspecting the belt.
If the belt feels loose, the fan motor should be moved further away from the central pulley wheel to increase the tension. In instances where the belt needs replacing, the component can be simply eased off the pulley wheel and a new belt fed around the outside of the pulley wheel instead.
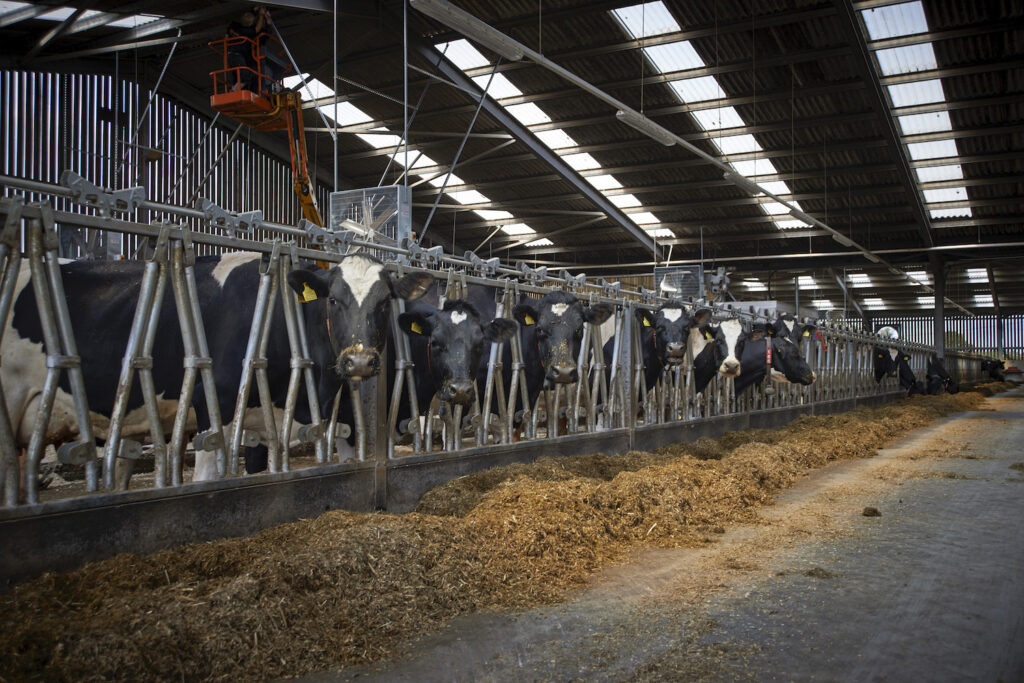
Futureproof solutions
For farms that don’t have ventilation systems in place already or are looking to retrofit their current setup, best practice is to consult with manufacturers like Hydor who can offer the optimum fan application for specific needs.
As an alternative solution, farmers should consider EC fans due to their enhanced speed control. Despite the higher capital outlay, there is the worthwhile benefit of using less electricity long term, as well as better and more equal airflow for internal surroundings.
Farmers can also deploy THI controllers as an ancillary, so that fans work at variable speeds in accordance with what the temperature and humidity at a given point. In effect, fans speed up and slow down to maintain ideal THI levels within the shed.
By adhering to maintenance processes and understanding the right solutions, farmers can be well placed to manage the impacts of heat stress. Ensuring peak production levels and optimum performance of ventilation systems can collectively result in more fruitful operations going forward.