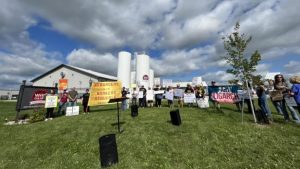
The cheapest and greenest unit of energy is the one we don’t use. In the era of record high energy prices, many farmers are now exploring renewable energy options on their farm. However, sometimes overlooked are the easy-wins.
Focusing on an ‘energy-efficiency first’ policy and reducing your overall level of energy consumption will quickly result in lowering your energy bills.
This week we kick off a new series focusing on energy efficiency on farms, beginning with dairy farms.
Ireland has a current milk pool of around 8.7bn litres which requires over 400 gigawatt hours (GWh) of electricity to produce. There is significant scope for Irish dairy farms to improve energy efficiency, reducing costs and greenhouse gas emissions, according to Barry Caslin, energy specialist with Teagasc.
The most obvious first step is to reduce energy wastage, ie fix hot water leaks, insulate hot water piping and refrigerant gas piping, switching to LED lights and using them only when necessary and make use of night-rate electricity.
Next, focus on energy use. Over 80% of energy used on a dairy farm is for milk cooling, water heating and vacuum pumping, so that indicates where to focus efforts.
Heating water
Heating water accounts for 23% of the energy costs on a typical dairy farm. Electricity is the most common method of powering water heating systems on Irish dairy farms.
Average figures suggest that a dairy cow uses 350 kilowatt hours (kWh) of electricity a year, of which 40% is for heating water.
The most common approach with electric boilers is to use night-rate electricity in combination with an immersion heater. It makes sense to synchronise the water heater with the night rate which is typically half that of the day rate.
Gas is also an efficient means of heating water but is dependent on grid access and prices are likely to remain high for the foreseeable future. For those still using oil, be sure to service the boiler regularly to ensure it is running at optimal efficiency. Heating water can be integrated with other processes on the farm to make best use of waste heat.
Milk cooling and heat recovery
Milk cooling is the largest source of energy consumption on Irish dairy farms accounting for over 30% of total use.
In many cases, milk is pre-cooled through a mains water plate heat exchanger to cool the milk before entering the bulk tank.
The cold water absorbs a portion of the heat, pre-cooling the milk.
Manufacturers generally recommend a water to milk flow ratio of 2:1, and as long as water is not being wasted, it can generally be said that the higher the ratio the better. In practice, the ratio on most farms will only be in the region of 1:1, however, so this is an area to focus on.
Cooling milk in the bulk tank releases heat via the condenser of the refrigeration unit. In some cases, this is evacuated into the air.
The refrigerant leaving the compressor of a milk cooling system is normally between 21ºC and 27ºC and this is energy that can be used to pre-heat water before it enters a water heater. In fact, the heat generated through cooling a litre of milk from 35ºC to 4ºC can heat a litre of water to 50ºC.
A heat recovery unit (HRU) transfers this energy from the refrigerant to water in a storage tank, raising the water temperature.
The most common type is essentially a large, insulated water tank that recovers heat from the refrigerant whenever the compressors run. The water heater is filled from the HRU, which in turn is fed by cold water from either the mains or a well. An HRU can pre-heat the water to 45ºC to 60ºC and can be retrofitted into existing installations.
Vacuum pumps
The vacuum pumps of a milking machine account for 20% of a total farm’s electricity consumption.
Variable speed drive (VSD) pumps can be applied to the vacuum pumps and these can dramatically reduce the electricity consumption of conventional vacuum pumps by over 60%.
Renewable options
Solar thermal
A solar water heating system has the following main components: collectors, which absorb as much heat as possible from the sun’s radiation; a heat transfer system made up of insulated pipework containing the heat transfer fluid; a water pump (which requires electricity); a heat exchange system; measurement equipment and a control system; and a water storage vessel.
The most common type of solar system used is a pressurised indirect primary circuit where the hot water from the solar collectors is pumped through a heat exchanger in the boiler to pre-heat the water. These systems have a long life with low maintenance. Many work reliably for at least 20 to 25 years.
On sites with high hot water demand, such as dairy units, the system can pay for itself two or three times over during its working life. Currently, solar thermal systems can avail of 40% TAMS grant aid or 60% for young farmers.
Solar photovoltaic (PV)
Solar PV just makes sense on dairy farms. With today’s energy prices and available grant aid, solar PV systems can pay for themselves within three to five years on dairy farms.
From 2023 onwards, TAMS grants will increase from 40% to 60% and it is understood that PV systems up to 30kW in output will be eligible.
Similar to other energy-efficient and renewable technologies it qualifies for accelerated capital allowances.
A useful add-on in dairy farms is a diverter which can divert excess electricity to heat the immersion tank (buffer tank) during off-peak times of the day.
This means that the immersion tank acts as a battery store to allow excess electricity produced at times of the day when it cannot be used elsewhere.
Top energy efficiency tips for dairy farms
-Ensure timer clocks are set correctly to make the most of night rates.
-Check the thermostat setting on water heaters and bulk tanks against the actual temperature of the water/milk.
-Ensure your refrigeration has adequate inlet and outlet ventilation and clean regularly.
-Check pipes for leaks.
-Insulate your water heater – a well-insulated heater will lose less than 5% of its heat compared with 50% from water stored in a bare copper cylinder.
-Insulate the first six metres of pipe running from the heater.
-Record energy use to benchmark against others.