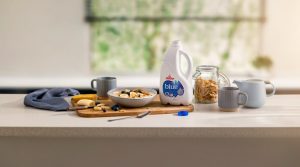
The process of turning manure into fuel is nothing new, but government incentives for curbing greenhouse gases have caused a boom in such projects, especially at dairy farms.
Since June, a facility north of Beresford, South Dakota, has been making renewable natural gas – or biogas – from the manure of 15,000 cows. It’s pumped from the large dairy farms into four giant, domed tanks called digesters, holding 2 million gallons each.
“Those digesters are 2 million gallons of the unwanted side of the cow,” said John Reid, plant manager at the biogas operation, owned by DTE Vantage.
The manure sits in the digesters for about three weeks, stirred and kept at a steady temperature of about 100 degrees. All the while, microbes break down the manure in an aerobic digestion process, releasing methane and other gases.
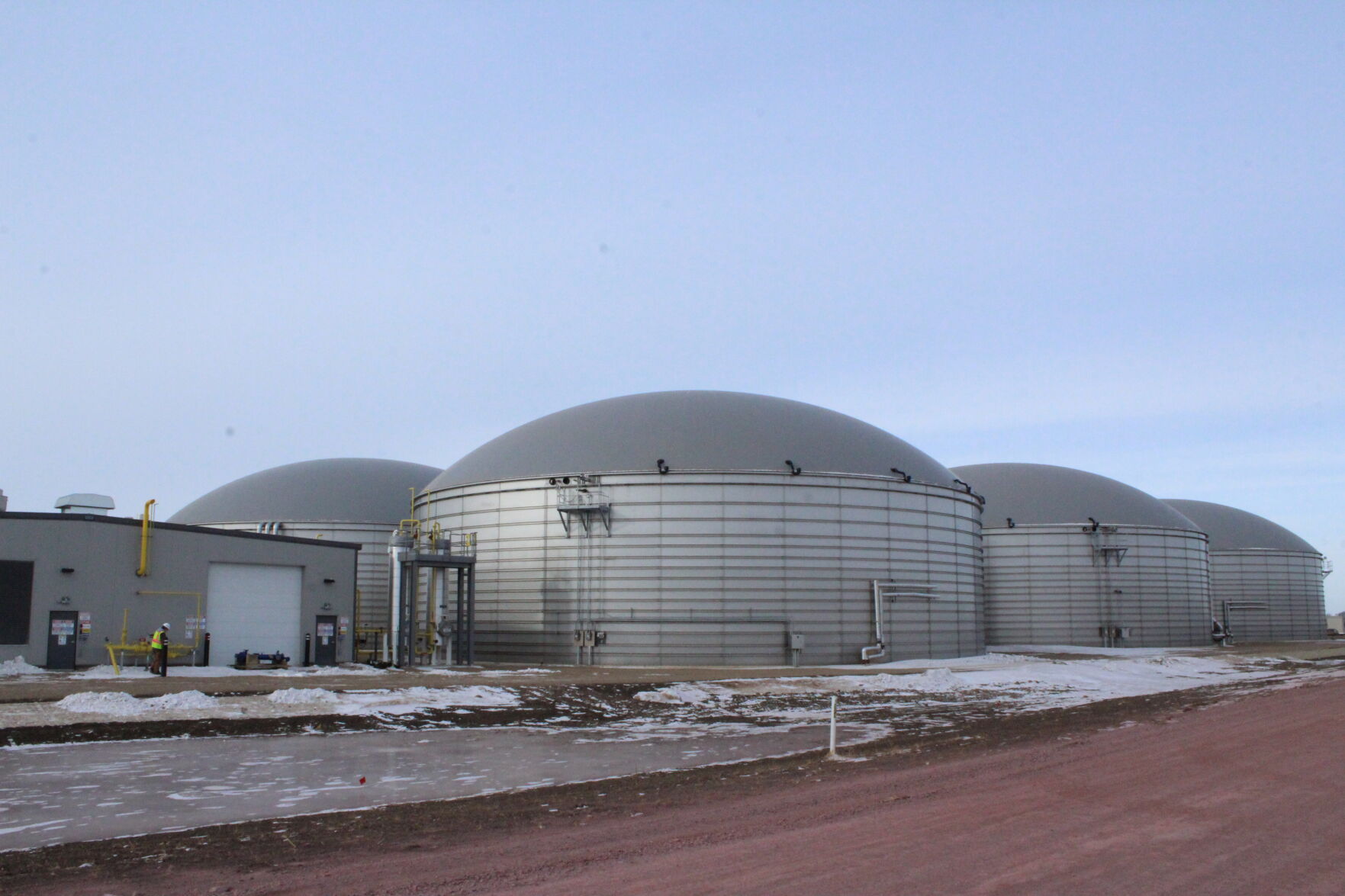
Tri-State Neighbor photo by Janelle Atyeo
In that sense, the term “digester” aligns appropriately with the biology of the animals whose waste is captured and reclaimed in the process.
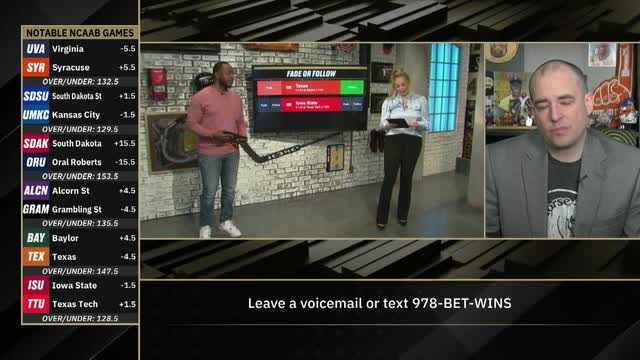
“We look at it as a cow’s fifth stomach,” said Dave Grooms, a facility technician and one of three full time employees at the operation.
Biogas is captured and refined on site. It can be used as electricity, heating fuel, or in the case of the Beresford operation, fuel for natural gas vehicles. Roughly 90% of the manure that goes into the digester comes back out with its nutrients intact. It can be used like any manure – as fertilizer for fields or bedding for cows.
Government incentives now offer a lot of money for digester operations in the form of renewable fuel credits. Dairy farmers are fielding a lot of phone calls from companies looking to build digesters, said Dr. Dan Anderson, an extension expert in agricultural and Biosystems engineering at Iowa State University who goes by @DrManure online. He’s taken plenty of calls himself from companies interested in working with Iowa State’s dairy, he told a crowd listening in on cattle topics at the Feedlot Forum in Sioux Center Jan. 17.
Iowa used to have four anaerobic digesters in operation. By Anderson’s count, that number has ballooned in the last year and a half to about 90.
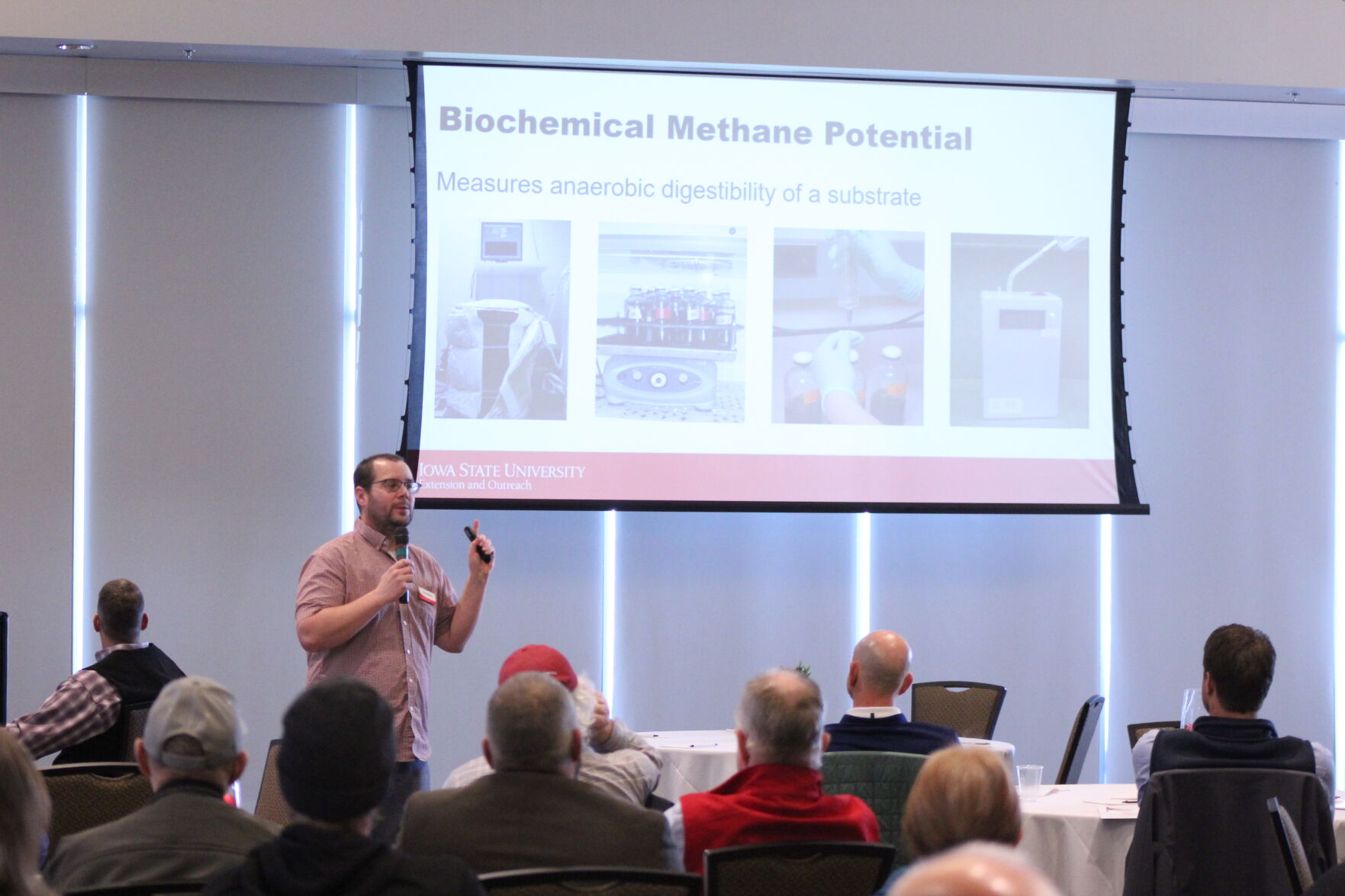
Tri-State Neighbor photo by Janelle Atyeo
“It’s a huge uptick in what’s happening,” he said.
Until recently, natural gas from landfills produced most U.S. biogas, according to the Environmental Protection Agency. Since 2009, POET has used natural gas from the Sioux Falls area landfill to power its ethanol plant in nearby Chancellor.
Ag-based natural gas projects have grown steadily over the last five years, surpassing the total number of landfill projects in 2021. It’s driven by policies such as the federal Renewable Fuel Standard, which requires a certain amount of transportation fuels from renewable sources like ethanol be blended with petroleum-based products. Some states, including California, Washington and Oregon have their own programs, like California’s Low Carbon Fuel Standard. Minnesota plans to propose its own.
Passage of the Inflation Reduction Act last year put biogas on par with wind and solar in terms of federal taxes for the first time.
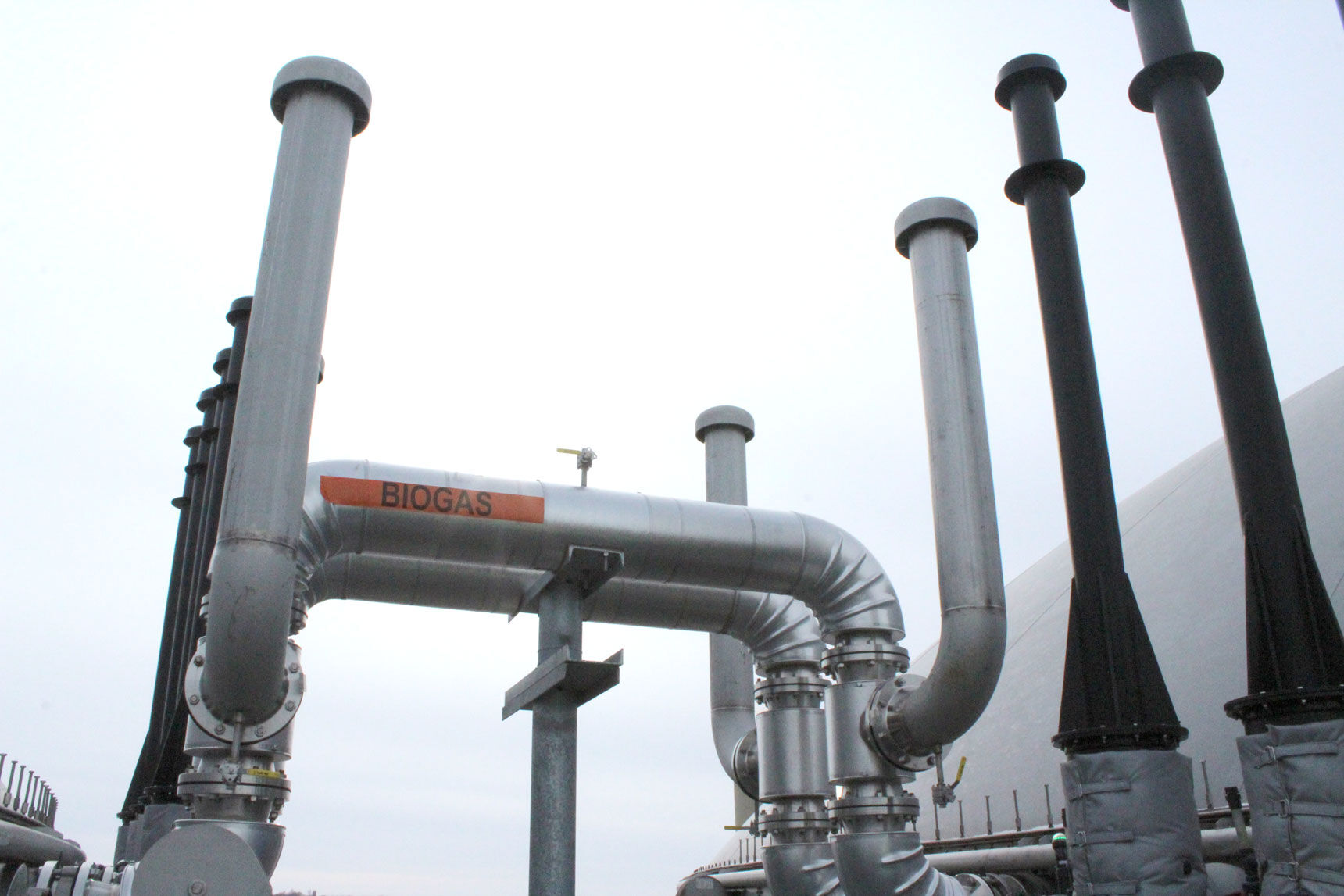
Tri-State Neighbor photo by Janelle Atyeo
Credits for biogas made from dairy manure can be worth up to $1,000 a year per cow, Anderson said.
Usually dairies partner with companies to build digesters. Because the companies take on most of the risk, the companies see most of the money. A digester costs about $1 million, by Anderson’s estimates. The system to clean the gas takes another half million dollars to build.The connection to major natural gas pipelines is a big expense, too, costing another $1 million.
A community of farmers would need to pool its resources to build biogas projects if producers hope to see a bigger bottom-line return, Anderson said.
“It needs to be big,” he said.
Can beef producers get in on the biogas trend?
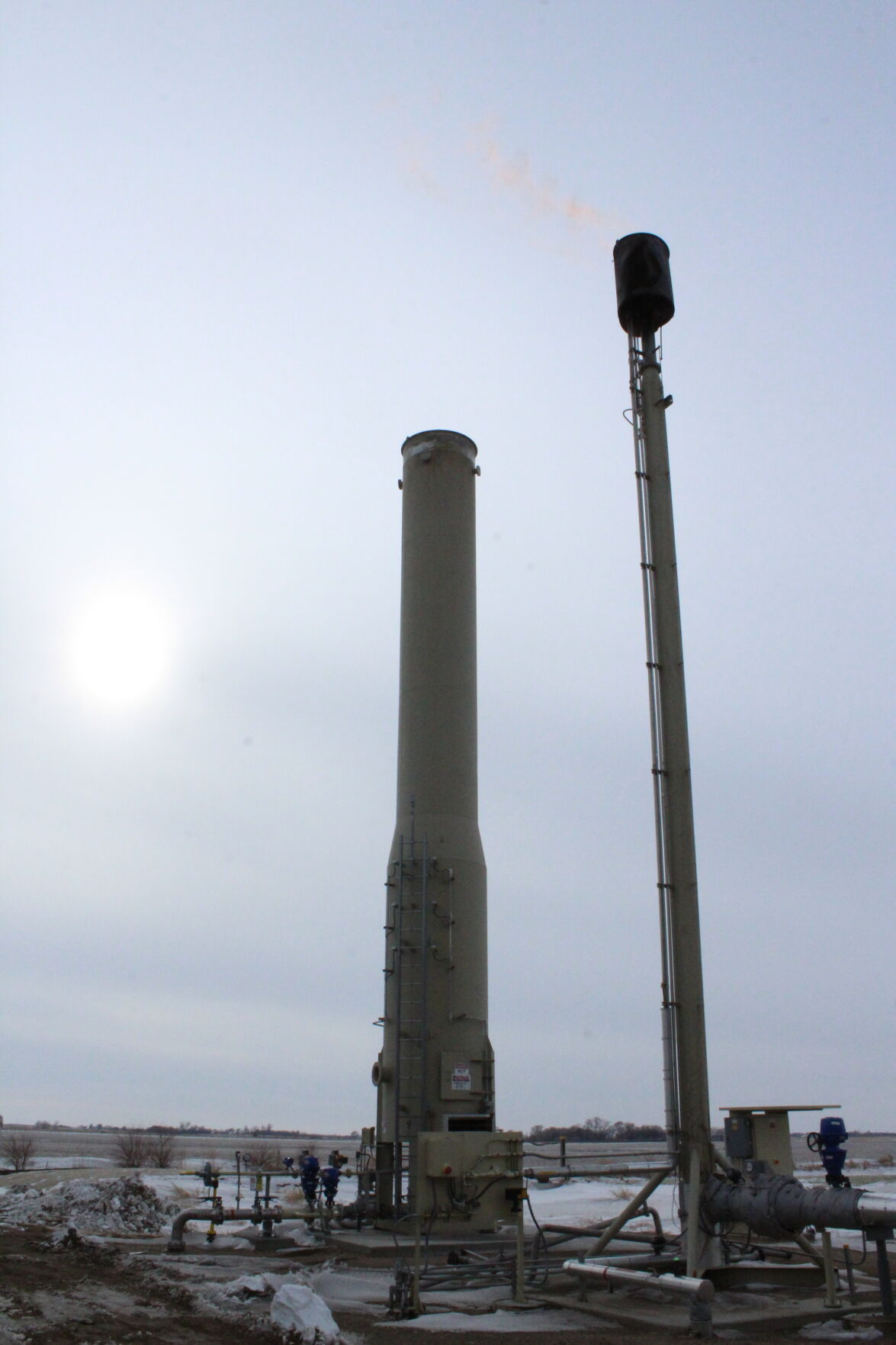
Tri-State Neighbor photo by Janelle Atyeo
It’s possible, Anderson said, though the type of manure treatment system matters. Anaerobic treatment works best with liquid manure, stored in a deep pit or lagoon, rather than solid manure from a feedlot.
Biogas from beef manure isn’t eligible for credits under California’s program. Only dairy and hog manure are written into the current law.
Because beef cattle don’t produce as much methane as dairy cows, federal credits from beef-made biogas are a fraction of the dairy counterpart. Federal Renewable Identification numbers (RINs) credits, through the Renewable Fuel Standard, are about $50 per headspace, Anderson said.
Where in the past, an anaerobic digester might have helped the dairy farm offset some of its electricity costs, today’s market adds a bigger financial incentive for these costly systems, said Dr. Erin Cortus, a University of Minnesota Extension engineer who’s worked with livestock and the environment since her days at South Dakota State University.
She said it’s important to consider the manure collection process, whether it’s scraped or flushed from the barns. Different systems influence which style of digester can be used.
Whether the dairy uses sand for bedding is another big question.
“We know how tough sand can be,” Cortus said. “It can be done, but it’s also a consideration.”
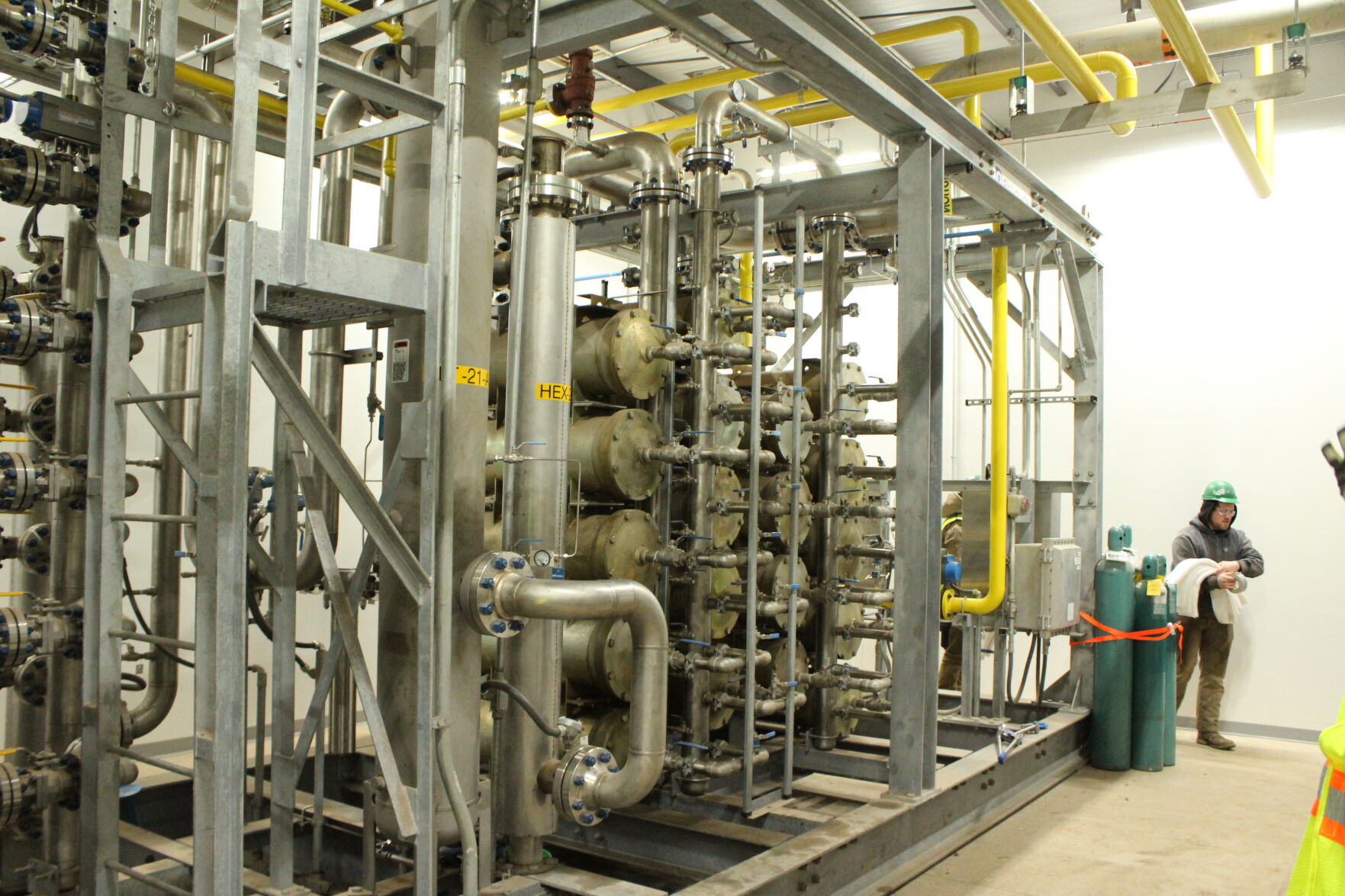
Tri-State Neighbor photo by Janelle Atyeo
Having physical space for the digester and manure storage are other points, along with access to a natural gas pipeline.
The biogas produced in Beresford travels 8 miles through a buried pipeline and meets up with a larger transmission line.
To join the pipeline, it has to be clean natural gas, and there are several checks along the way to monitor that. At the Beresford facility, the gas moves through a system of membranes and heat exchangers to clean out water and oil. Unwanted gases, hydrogen sulfide and carbon dioxide, are burned off in two on-site flares.
“We’ve been taking bad gas … and cleaning it up, taking waste gas from landfills since the 1980s,” said Kevin Dobson, vice president of biomass for DTE Vantage.
A few years ago DTE started working with dairies in Wisconsin. The Beresford facility is the company’s first in South Dakota, and Dobson said they hope to do more.
The two large dairy barns with 15,000 cows between the two made the Beresford location attractive to DTE.
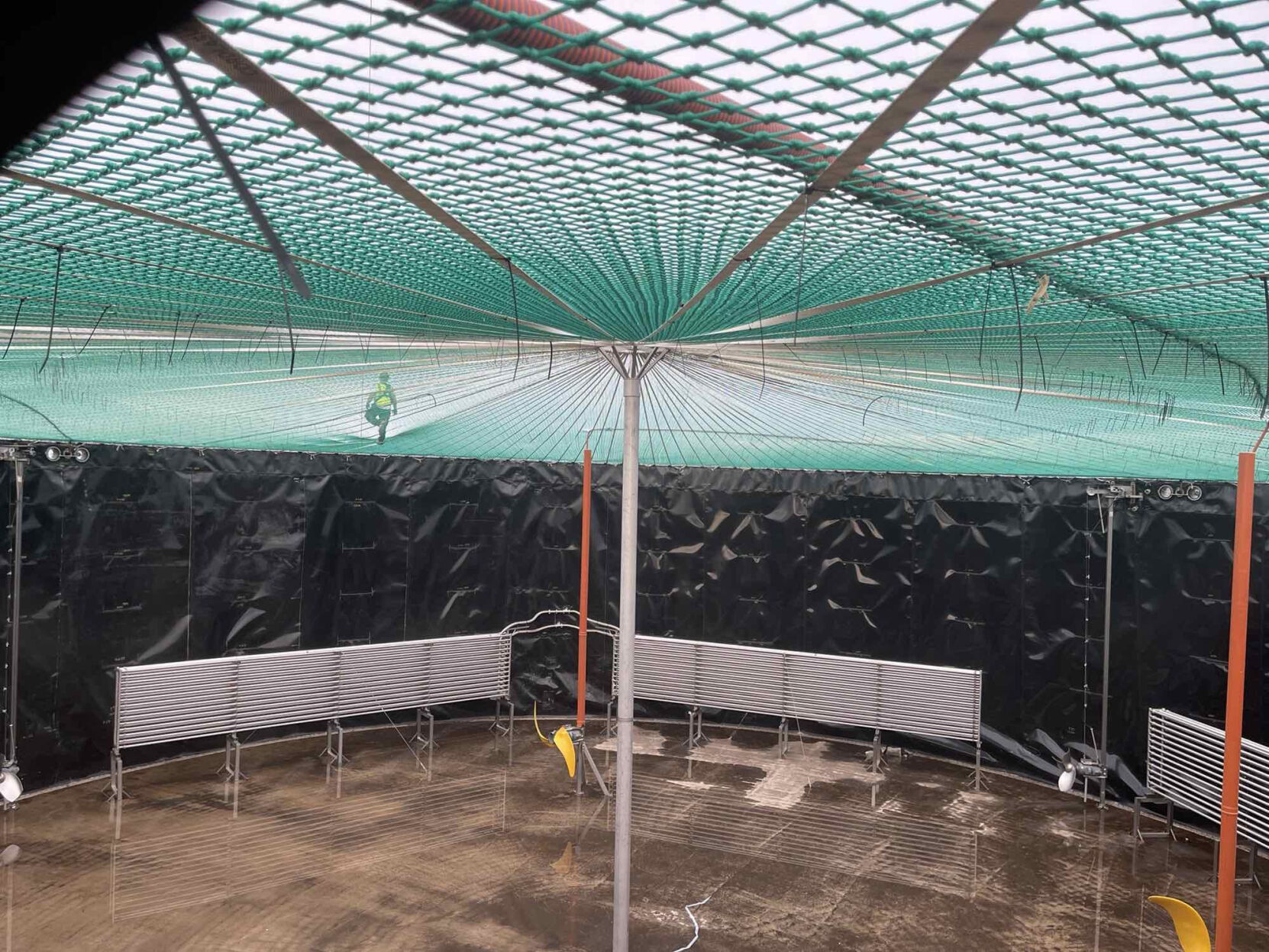
Submitted photo
“These are pretty expensive projects to build and maintain, so we wanted size for an economy of scale,” Dobson said. “The location is nice, and the farm is a very good partner.”
The Beresford dairy owner asked not to be named for this story.
The farmer is compensated by DTE, and still gets to apply the manure to fields as fertilizer.
“There’s the incentive in compensation that’s not tied to the milk market,” Dobson said.
There are also environmental benefits, he said. Capturing the natural gas reduces greenhouse gas emissions from the farm. It can also help improve water and air quality around the farm, Dobson said. The manure that’s left after the natural gas removal process, called digestate, has less of an odor than raw manure, Dobson said, and fewer fecal pathogens, making it better for water quality.
Like DTE, another digester company, DVO Inc., got its start in Wisconsin in the mid-1980s. An early DVO project involved Gordondale Farm in Wisconsin, which was being sued by neighbors because of the manure smell, said DVO planning engineer and president Stephen Dvork.
Dvork gave a presentation last month at the Minnesota Renewable Energy Roundtable hosted by the Agricultural Utilization Research Institute in Waseca.
He spoke about the benefits of using digestate as fertilizer, which in Wisconsin is sometimes applied through irrigation systems. Manure can be applied directly to the crop without burning it, he said, and many of their customers have stopped buying lime because the digestate has high pH levels.
Cortus urges producers to test digestate before application, as they would with any manure. In theory, nutrients in digestate are more readily available for plants to use.
Her U of M Extension counterpart Melissa Wilson discussed the nutrient content of digestate at the Renewable Energy Roundtable. Typically, digestate is higher in ammonium nitrogen, which is more plant-available than typical raw manure.
“Total N, P and K remain stable, but these nutrients are changing their forms,” Wilson said.
Many farmers add another step to processing the digestate and separate the liquid and solids. That can be beneficial when applying manure with precision technology, Wilson said. The liquid has little phosphorus, but is a much better nitrogen and potassium source. The solids have more phosphorus.
“It becomes a very high value fertilizer,” she said.
Standing by the inner workings of the Beresford biogas system he manages, Reid reflected on how they are taking methane, a gas that’s been a target in efforts to clean up the environment, and turning out products that can replace fossil fuels and synthetic fertilizer.
“It’s a cool thing to be a part of,” he said.