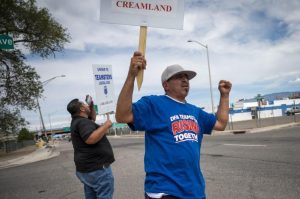
Cow comfort and consistent, quality nutrition are the focus of what makes top-quality milk, according to brothers Brad and Mark Crandall, who are milking 350 cows in Calhoun County, Mich., just a few miles outside of Battle Creek.
This fifth generation of dairymen farm in partnership with their father, Larry, who is semi-retired, and they were recently awarded the highest honor in their industry. Crandall Dairy Farms received the Platinum Award in the National Dairy Quality Award program for consistently producing the highest-quality milk.
The program considers somatic cell count, standard plate count data and other quality standards. Crandall Dairy has a rolling herd average of about 32,000 pounds and somatic cell count in the 60,000s.
The Crandall family received the award at the National Mastitis Council’s annual meeting in February in San Diego. It is their fifth national award, but their first at the platinum level. At the state level, they have received 10 straight gold awards from their co-op, Michigan Milk Producers Association.
Crandall Dairy is a centennial farm first established in 1883. It is also home to 240 head of young stock.
High-quality forages are raised on 800 acres of mostly family-owned land, all within 2 miles of the farm. “That’s been a huge advantage for us when bringing in feed and hauling manure,” Brad says. “And we harvest all our own crops, which means we can harvest forages when it’s optimal.”
The family works with a nutritionist to balance feed rations on the computer. All corn silage and haylage is produced on the farm, except for soybean meal and canola.
“We normally feed mostly canola, but right now, with the climate of what’s available, we’re feeding soybean meal as our main protein,” Brad says. “We also raise a good percentage of corn we feed. We store it at the elevator and bring it back to the farm.”
Sand is used for bedding, and milkers clean the 48-inch-wide stalls daily. “When it’s warm, we run water on the cows when they are in the milking parlor,” says Brad, 51, whose wife, Monica, handles the farms accounting and works at a nearby elementary school.
Farm history
Brad and Mark’s grandparents, Frank and Bernadine, decided to focus on dairy in 1957 when they built a double-six, swing parlor — one of the first dairy parlors in the state.
“They had the forethought of putting in a more modern, ergonomic system that made day-to-day milking easier, which was a big advantage to the farm,” Brad says. “With all the other challenges in dairy through the decades, having the parlor instead of a stanchion barn probably kept us in business.”
Brad’s father, Larry, earned a degree in dairy science from Michigan State University and brought back nutrition concepts to the farm, while expanding the herd to 160 cows. But growth wasn’t the only objective.
By hiring quality employees (two full-time and a dozen part-time workers), retaining them and motivating them to care about the details, it allowed the farm to focus on improvement.
“Many core operators are trying to do so many everyday chores, they don’t have the opportunity to focus on nutritional advancements and genetics like we did,” Brad says. “We were early adopters of artificial insemination. And bigger isn’t always better. For a long time, cows kept getting bigger. Mammoth cows give a lot of milk, but they also eat you out of house and home and are more prone to injury.”
Cow comfort
After earning a degree from Michigan State in ag business and supply chain management in 1994, Brad pondered his career path. He decided to return to the farm, putting great attention on cow comfort.
The transition between generations has been slowly happening, as were investments. “It was clear the operation was being held back by older facilities that didn’t fit the needs of today,” Brad says.
Little by little, they added modern buildings, starting with new heifer facilities that allow groups of six to 10 younger heifers to move from pen to pen down the line.
“Before we built that, we had makeshift pens in other buildings used for other purposes,” Brad says. “It was kind of a circus, having to set up temporary gates or trailer them around from pen to pen. This new system is so much more efficient, which allows us to feed them properly.”
The calves were in a classic hip roof barn in pens. “It wasn’t a very healthy environment for them,” Brad notes. “So we started with calf hutches, and now we’ve built a modern calf-raising setup.”
In 2001, they built a four-row freestall barn holding two groups of 120 cows, a third group of about 80 first-lactation milking cows, and the fourth quarter of that barn is dedicated to dry cows. They switched from a mechanical feeding system to drive-by feeding. And while the 1957 parlor was functioning, it was still in the hip roof barn, so they replaced it with a double-12, parallel milking parlor in 2013.
“Every building we built in the last 30 years has curtains on the side and doors to open in the summer, as well as fans,” Brad says. “More than anything else, the ventilation has been a huge improvement.”
With the addition of the freestall barn, the farm went from two- to three-times-per-day milking. “In that first year, we won the Dairy Farm of The Year Award through our DHIA service, because we increased our production 5,000 pounds [of milk] a cow,” Brad says.
The manure pit was expanded, and an older barn was renovated into a maternity pen.
‘Sharpening the stone’
The Crandalls currently are not looking to grow the operation — cow-number wise. “With the land we have, everything works fairly efficiently,” Brad says. “By adding more cows, the system doesn’t work together. We’re more about sharpening the stone and being more efficient.”
One area of potential expansion is with technologies. One they adopted last fall is an ear tag, cow-monitoring system called Cow Manager. All the milking cows have them, as well as breeding-age heifers.
Through a phone app, the family receives alerts about cow activity and health. “The tags monitor their temperature and detect motion in the way they move their head when chewing cud, which is a good indicator they’re feeling good,” Brad says.
There is a per-tag initial fee, as well as a cost for access to the cloud-based, Wi-Fi system. Antennas are set up around the farm, and every hour, data is pulled in from the tags.
Brad likes the milk-quality awards because they recognize everything that goes into milk production — from feed and animal care to dedicated employees and farm management.
People are really hungry for food-quality information, Brad says. “Many are skeptical, but if you’re looking for the good, you might be surprised at how much of it is out there,” he says.
Being efficient and productive, while producing the highest quality of milk, can all be done at the same time. It’s not give or take, Brad says.
“People need to know those things actually go together,” he says. “You don’t get hugely efficient without taking good care of the animals.”
Mark has three daughters, while Brad and Monica have two daughters and a son. All have helped on the farm, but Zach, 20, is the only one potentially interested in carrying on the dairy. He is currently in a diesel tech program at Northwest Ohio University.
“We may be trying to expand our land base,” Brad says.