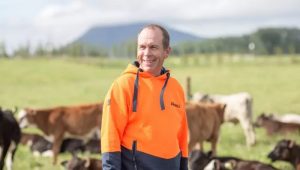
Milk let-down can only be capitalised on if the machine infrastructure and settings are sufficient to cope with high milk flow.
Maximising flow through the machine is important, not just to achieve a swift milking, but also to optimise the conditions that the cows’ teats are exposed to.
Vacuum at the teat end is the result of system vacuum minus any leaks and losses. If the machine moves milk away from the teat efficiently, this vacuum will remain constant throughout milking.
However, if the milking machine struggles to cope with high flow rates from the cow, the vacuum at the teat end will drop (see graph below © Advance Milking).
Milk flow from the cow
Poor milk flow away from the cow will lead to lower teat-end vacuum and cause:
- Lower compressive load on the teat when the liner is collapsed
- A shorter resting phase caused by the liner opening earlier and closing later
- Increased risk of teat-end oedema
- More opportunity for “re-spray” of milk rinsing the teat
- A smaller vacuum gradient between the base of the teat and the liner below
- Slower milkings and greater udder infection risk
Improving milk flow away from the cow can reduce or eliminate the drop in vacuum and associated problems.
Detecting problems
The challenge in detecting flow issues is that our normal static test does not give a reliable prediction of how the machine will function with milk running through the system.
Some issues can be checked by visual inspection, but to assess the impact of these factors on teat-end vacuum a dynamic milking time test must be performed.
Areas to check
If an issue with milk flow is detected, the key solutions are based on mixing air into the milk, optimising formation of “slugs” of milk in the long milk tube and reducing any restrictions in the milk path.
To work out which solution is appropriate, six areas need to be looked at:
1. Liner properties
Liner dimensions should provide a good fit to reduce risk of teat swelling. Compressive load should be sufficient to counteract teat-end oedema.
Vented liners introduce more air into the milk, improving flow through restrictions.
2. Claw piece
Flooding of the milk claw bowl presents a ‘barrier’ to vacuum reaching the teat. Using a bowl with a larger volume can help improve flow at teat level.
Blocked air bleeds (or even small-diameter bleed holes) reduce the air content of the milking and impair flow from the bowl. To avoid this, keep them clean and watch for excessive milk falling from the cluster at detachment.
3. Long milk tube
Milk must form slugs to travel through the long milk tube, particularly in highline or midline systems.
The diameter of the long milk tube affects flow: too narrow, and there is increased resistance; too wide, and the milk may not fill the tube to form a slug.
While slugs are necessary, if they are too big, they can hamper flow. Large, drooping loops of long milk tube increase slug size, reducing milk flow and act as a barrier for the vacuum reaching the teat.
4. Milk path
Changes from wide pipe to narrow pipe will restrict milk flow. Bends of 90deg or 180deg will significantly increase resistance, especially if the radius of the pipe at the turn is small. Kinks in soft tubing will also interfere with flow.
5. Intentional disruptions
In-line filters substantially increase turbulence, acting as a barrier to vacuum being transferred further through the long milk tube.
Milk-sampling ports will have a similar effect if left in place permanently. And even milk meters can impact on milk flow rates, affecting vacuum at cow level.
6. Plant design
Milk line height is a key factor in how challenging it is to move milk away from the cow: the higher the line the more likely we are to see problems with milk flow.
Pulsation type can affect milk flow, for example, 4-0 pulsation increases the amount of milk that needs to be moved through the claw piece and long milk tube at any one time.
Flooding of the milk line is disastrous for vacuum at cow level and can be caused by too many milking units entering a single line, insufficient pipe diameter or incorrect slope.
Vacuum reserve and regulator position may affect the ability and speed of the system to respond to changes in vacuum at cow level.