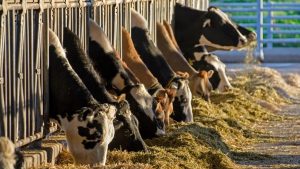
Water flowing down the river would turn a water wheel, which would power a drive shaft. This main drive shaft would power things like a millstone to make flour or a cutting blade to saw timber.
Belts or gears would engage the main drive shaft and direct rotational power to individual pieces of machinery.
When the steam engine arrived this enabled more options on where a factory could be built. Running water was not required, just access to coal or timber.
But the factory design was still built around a central drive shaft, it was just powered by a giant steam engine instead of a water wheel.
The location and configuration of equipment was determined by how each machine could access the main drive shaft.
In a manufacturing environment, a component may need to be pressed, hammered and then drilled. But the press, the hammer and the drill could be in three separate rooms as that was the only way each machine could access the central power shaft.
There was lots of time wasted running components back and forth between equipment. Because the main design consideration wasn’t manufacturing efficiency, it was access to the drive shaft.
Eventually, factories began replacing their big steam engines with electric motors.
These early adopters placed the electric motors in the same room that had housed the steam engine. The motors just powered the centralised drive shaft in the way they had always done and the efficiency gains were minimal.
They were using the new technology but with the old way of thinking.
The power plant to drive equipment had always been a big centralised power plant like the river or the steam engine.
They couldn’t conceive that each individual piece of equipment could have its own power plant. The concept of a handheld tool having its own motor was unimaginable.
The true benefit of the electric motor was that power could be located anywhere in the factory. The power source had transitioned from being a centralised resource to becoming a decentralised resource, that could drive individual equipment.
This may seem insignificant to us now, but it was a change that enabled things to be done in completely different and inconceivable ways.
Machines could now be located in the order that made sense for the manufacture of each component. The press machine could now be located next to the hammer which was next to the drill.
The obvious extension of this was the assembly line.
Henry Ford had developed the basic assembly line in 1909 without the adoption of electric motors. But Ford quickly made use of electric motors and developed overhead cranes, conveyor belts and electric wrenches – equipment that would have been considered science fiction 10 years prior.
The first Model Ts produced in 1909 were already 20 per cent cheaper than the competition. But in the following years, Ford refined its assembly line to be more efficient.
By 1920, the Model T was selling for 63 per cent less than it was in 1909. The huge productivity increases were realised via a combination of standardised parts, assembly line production, simplified design, and a desire to not do business as usual.
Underlying Ford’s innovation was electricity and the electric motor which enabled them to develop new ways of doing things.
Today the game-changing technology is the internet. It feels to me we’re largely using the internet with the old world way of thinking. We’ve just swapped a steam engine for an electric motor.
Trade Me is a bit better than the buy/sell and exchange paper, Netflix is a bit better than the DVD store, online shopping is a bit better than the mail-order catalogue and it looks like we’ll still need a satellite dish to watch the next Rugby World Cup.
But where the internet has made a dramatic difference, is that it has allowed us to digitise more things. When something is digitised, it goes from being a scarce resource to a plentiful resource and its price plummets.
The digitisation of music and photography are two examples.
At the Happy Cow Milk Co, we’re attaching the internet to milk processing equipment. The result is, we’re able to digitise the regulatory compliance of dairy processing.
When the cost of compliance goes to zero, it changes what a milk factory can look like. It enables milk processing to go from being centralised in big factories to becoming decentralised.
Just as the idea of an electric hand drill was inconceivable in 1880, the possibilities that decentralised dairy processing brings to the milk business may be hard to imagine.
It means a 16-year-old can milk her five cows after school and legally sell the milk. It means you can become an ice cream maker on your kitchen bench and sell it legally.
It means things can be done in an entirely new way, which is what the internet is for.
Glen Herud is the founder of the Happy Cow Milk Company.