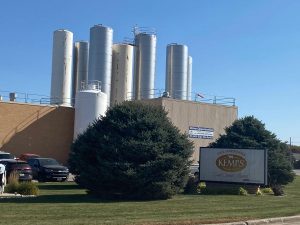
The magnitude of the expense drives dairies to increase labor efficiency. The thought is that if we increase the efficiency of the labor on our dairy, the total labor cost of the operation will decrease. However, this is not always the case. This is because labor efficiency does not equate to labor productivity.
Now this may seem like a distinction without a difference. However, when it comes to many of the positions on the dairy, there is an evident difference. Let’s look at the feed center as an example. Bigger loader buckets, larger mixer wagons, automation and batching systems are utilized to make the feeder more efficient and reduce the time they spend feeding. If, instead, our aim is to increase the productivity of the feeder, the point becomes to increase the output of feed in a fixed amount of time. The key is in the fixed amount of time. The feeder, just like many other jobs, will work an eight-to-twelve-hour day. In many cases, it does not matter if they can feed in five hours, they will fill the time in which they have. It was put simply for me once when I asked, “How long does it take your feeder to feed?” The reply was simple, “As long as we give them.”
How do we then encourage greater productivity versus driving efficiency? Some of this depends on the farm size and organization, but a clear option would be to add more responsibilities to the employee’s role. Using the feeder as an example, perhaps they begin collecting their own weighbacks or uncovering the forage piles on top of their feeding responsibilities. This could also be called cross-training. Cross-training employees, especially in small-to-mid-size operations, is a great way to increase labor productivity.
A second key to increasing productivity across the operation is to increase the “up-time” of all tasks. Up-time normally refers to the time machines can function. In terms of labor productivity, it is the amount of time employees are completing productive work. This may be perceived as limiting breaks and distractions for employees, however, it is about us, as managers, creating the workflow for employees to lessen the time between productive tasks. For the feeder this entails having functioning garage doors, opened cross-alley gates, and feed deliveries scheduled for the end of the day.
The final way to increase productivity is through specialization. Specialization is the opposite of cross-training. In this way, for specialization to become a useful means to achieve productivity, the operation must be large enough for the specialized task to fill an entire shift. In the feed center, this may look like dividing the feeding task into a loader driver and a feed delivery driver.
For dairies of all sizes to decrease their labor costs, continue to shift the focus from efficiency to productivity.