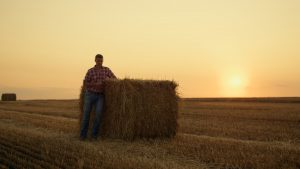
New dairy building designs are popping up across the province, that are shorter, sleeker and looking like they are wearing tinted glasses.
Tunnel-ventilated free-stall barns have become more common over the past few years as a new design has come to dominate tunnel ventilation.
Why it matters: Cow comfort is key to dairy farm profitability and some farmers have decided that tunnel ventilation in larger barns is the best way to keep cows cool and to reduce flies.
At Lorenz Guntensperger’s farm near Seaforth, a new barn with room for 330 animals employs tunnel ventilation to keep it cool.
Twenty-six fans at the end of the barn suck air down the 460 feet of the barn from the large door openings at the other end.
The location of Guntensperger’s new barn doesn’t make natural ventilation an option, as another farm is nearby. The new barn is near the house, and having the ability to draw odours and insects down and out the other end of the barn was attractive, he said during an open house at the barn.
His barn, along with another barn, run by the Van Hittersum family, north of Blyth, held open houses recently. Both were built by Dairy Lane Systems.
The tunnel ventilated barns have more consistent air flow than some of the other designs — such as the taller side-walled barns with ceilings that have been a standby in the Ontario market for years.
Tunnel ventilation isn’t new, says Mike Van Logtonstein, of Dairy Lane Systems, as strategically placed fans helped bring fresh air to older tie-stall barns over the past couple of decades.
Tunnel ventilation faded from popularity as more free-stall barns were built that are naturally ventilated through curtains on high sidewalls. Other fans were required and were often large, slow speed fans that were energy efficient, but also could result in air dead zones in the barns.
Some farmers then moved to more box fans in the barns raised above the cows, which have helped but have increased energy costs.
The new design, mostly built with steel framing set at 20-foot intervals have no ceiling as the tunnel ventilation, along with chimney fans that operate in the winter, reduces concerns about condensation. Wood purlins fit between the steel cross beams.
The barns go up quickly, says Justin Mulder of Dairy Lane Systems.
The cost of the steel-frame, tunnel-ventilated buildings is about the same as a naturally ventilated free-stall barn.
At the Van Hittersum farm, the barn is 105 feet by 340 feet, with an almost completely open end on the inlet side of the barn. At the other end, 28 fans pull air through the barn at 600 cubic feet per minute, changing the air in the building every few minutes.
The barn is mostly closed up during the winter, says Kevin Kraemer of Dairy Lane, with air coming from inlets higher on the inlet wall, and as well around the edges of the panels that cover the sidewalls.
The sidewalls are one of the greatest visual differences between traditional free-stall barns and the new design of the tunnel-ventilated barns. Sidewalls in naturally ventilated barns are around 18 feet, whereas the tunnel ventilated barns have 12-foot sidewalls. The tinted polycarbonate panels are fixed, compared to the moveable curtains on the sides of naturally ventilated barns.
Think of it as sunglasses for barns.
“It lets in natural light, but reflects heat out,” says Van Logtonstein.
Guntensperger says he was intrigued by the first tunnel ventilated free-stall barns he saw in the province, and was convinced to try it out for himself when the first builder of one of those barns decided to build a second.
Overall, he says there are fewer fans than he’d need to get similar air movement in a naturally ventilated free-stall. However, the fans that are there at the end of the barn will need to work more hours. As a result, there will be an increase in energy costs.
“It gives you a more controlled environment year round,” says Guntensperger.
More energy may be required in naturally ventilated barns in the summer, but then during spring and fall, the tunnel-ventilated barns will use more energy, as the system aims to maintain a similar environment over the year.
Guntenperger has been milking in the new barn for about five months and he says the barn performed well over the summer, with no bunching of cows, as can happen in barns where there are areas with more ventilation than others.
“The cows seem to handle the heat better now,” he says, adding that the cows recover from hot days over night well.
Fewer flies are another reason Guntensperger says he likes the barn. The fast-moving air keeps them from settling in the barn.
Once barns get to 600-feet long, the ability to drag the air that far down the barn is less, says Von Logtonstein. Larger barns need to be cross-ventilated, with large numbers of fans pulling the air across the cows from openings on the other side.