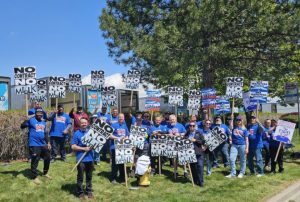
Day in and day out, tanker trucks pull into Organic Valley Creamery’s newly enclosed loading bays to deliver milk from organic dairies in Oregon, Washington and Idaho. Often they pass trucks leaving with huge totes of powdered milk or tanks of cream destined for other plants that use it to make butter.
Butter once was made at the McMinnville creamery, which sits at 700 N.E. Highway 99W in the middle of town. But butter production has been suspended since fire destroyed much of the facility on April 20, 2021.
“Our next challenge is strategic,” said Mark Pfeiffer, vice president of internal operations based at Organic Valley’s Wisconsin headquarters.
He frequently visits the McMinnville site, the former Farmers Co-op Creamery that Organic Valley converted to an organic powdered milk and butter plant in 2017. On May 11, he toured the plant with Jeff Frank, the cooperative’s new CEO, who was making his first visit since being named to the position this year.
“What will the world look like?” Pfeiffer asked, pondering the future of butter consumption, as well as the needs of the cooperative’s member dairies and the costs of resuming butter production here.
Those factors will have to be considered before Organic Valley can decide what phase two of the McMinnville plant will include — butter, alternative packaging for milk powder or other products — and when, or if, that phase will get underway.
But they are pleased as can be about phase one, a $32.5 million project which restored the plant to accepting and processing milk just a year after the fire.
“We sprinted hard,” Pfeiffer said. “I can’t say enough about the city, our team and the contractors.” Crews broke ground in October 2021 and had much of the plant up and running by early spring 2022.
The new enclosed loading bays are an important part of the operation. They allow milk to be unloaded quickly and comfortably out of the weather and in more sanitary conditions. Milk from each tanker is screened for quality prior to unloading, as well.
“We could do 24 million pounds of milk a month,” said Paul Silva, maintenance manager. That would be about 2.8 million gallons.
Two more towering tanks rise high above the buildings, increasing storage capacity from 1.2 million gallons prior to the fire to the current 1.8 million.
The stainless steel tanks give the plant not only more room, Pfeiffer said, but also provide separate areas for various fluids, such as 100% grass-fed milk, regular organic milk, cold-pressed, and cream.
Soon after the fire, before a decision about rebuilding was announced, Organic Valley bought the additional tanks used, Pfeiffer said. Without that forethought, he said, the creamery might still be waiting to receive new tanks; it couldn’t have reopened nearly as soon as it did,
In addition to storage, a new, larger lab allows for more efficient testing in-house. “It’s a big upgrade,” said Scott Fields, manager of the McMinnville site.
Workers screen each batch again to make sure it is free of antibiotics and bad bacteria. They check for odor, temperature, bacteria levels, added water and other characteristics, getting immediate results, Silva said.
He appreciates the new lab. It’s one of many improvements he’s seen since he joined the creamery in November 2000, long before it was purchased by Organic Valley.
The most remarkable parts of the first phase, however, may be the things that survived the fire. In addition to the two tanks, several key pieces of equipment were returned to use after cleaning and restoration.
Large heaters surround pipes through which the skim milk flows, heating it up and pasteurizing it. In the same room, a giant separator spins, sending the heavy cream one way and the lighter milk another.
All were pulled out of the rubble following the blaze. Pfeiffer praised McMinnville firefighters and those from other departments for their efforts that Tuesday, as well as over the next several days when things continued to smolder.
“They worked hard to preserve our assets,” he said.
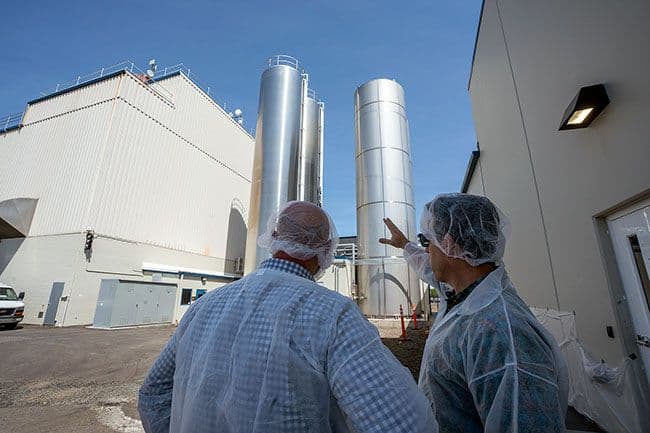
Organic Valley company officers Mark Pfeiffer and CEO Jeff Frank look at the huge storage tanks saved from the fire and new ones added in the reconstruction of the McMinnville plant. The company ordered additional tanks soon after the April 2021 blaze, which helped expedite rebuilding, allowing it to return to dry milk powder processing a year ago.
They even saved an evaporator/dryer area at the front of the property with its signature mural on its west side. Farmer Melissa Collman of Cloud Cap Dairy still smiles down at traffic on Highway 99W.
The blaze affected about 46 workers in McMinnville. Some, such as Silva, kept working during the post-fire cleanup, planning and rebuilding process. Others received compensation and assistance with finding other positions; most said they valued working for Organic Valley and hoped to return, Fields said.
About 26 or 27 work on site these days. If phase two goes up, more will be added.
The blaze also left Organic Valley’s 59 West Coast member farms without a place to take their milk.
The company arranged for milk to be trucked to other creameries in Washington, Idaho and California for the time being. By mid-summer, the McMinnville property was serving as a transfer site to accommodate this process.
Since Phase I opened a year ago, Willamette Valley farmers such as Steve Pierson and Jon Bansen have been glad to be able to ship milk to McMinnville again.
Every day the organic milk rolls in, double tanker by double tanker. It’s pasteurized, separated into cream and skim, and the latter is dried to make what the dairy industry calls “NFDM,” or nonfat dry milk powder.
The powder is loaded into totes that hold 2,000 pounds for sale to companies that use it in making yogurt, ice cream, fortified milk and other dairy products.
McMinnville’s creamery used to package milk powder into 55-pound bags, as well, for customers who couldn’t use so much at a time. But the bagging line was lost in the fire, Pfeiffer said.
New equipment and a new building to hold it would be needed to resume selling the powder in smaller quantities.
That’s one possibility for the second phase. Or the creamery could put in the equipment to produce whole milk powder, as well as skim.
Or it could be butter making facilities, which Pfeiffer estimated could cost $40 million.
Pfeiffer said the board, made up of farmer members, will be considering Pfeiffer’s earlier question: “What will the world look like?” Will consumer demand for organic butter increase as health-conscious consumers embrace natural products? Or will those same consumers eschew fats entirely?
The board is expected to have its answer soon, possibly in June, he said.