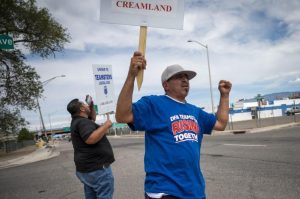
How refreshing I found it to speak with Denise Barstow Manz, the engaging scion of a family of brilliant entrepreneurs who have been operating a successful dairy farm in western Massachusetts for seven generations.
To help you place the innovative Barstow’s Longview dairy farm in historical context, Denise’s family has been farming in Hadley since Hamilton played on Broadway (not the Lin-Manuel Miranda musical… the actual powder-wigged duelist founding father himself*).
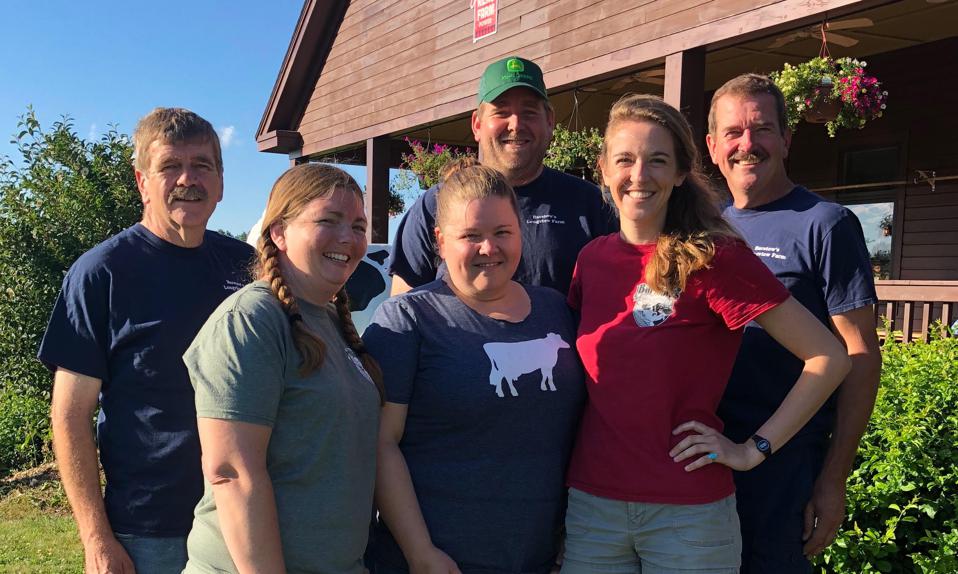
BARSTOW’S LONGVIEW FARM (HTTPS://WWW.BARSTOWSLONGVIEWFARM.COM/)
Farming has never been easy. Since the early 1970s, farming on a small plot of land has been growing harder and harder due to changes in government policy that favored large, industrial farming operations.
Barstow’s Longview Farm, which Barstow Manz characterizes as “medium-small,” is home to 600 head of cattle—300 of which are milking cows and the remainder are young stock and calves who will become part of the milking herd when they are older—on 450 acres of land that supplies forage for the whole herd.
To put the Barstow 300-head herd size into context, the USDA reports that in 1987, the median dairy herd size was 80 cows. Thirty years later, in 2017, the median herd size had swollen to 1,300! The economics of dairy farming favors larger manufacturers that concentrate production in a single geographical area and deliver the milk and dairy products using distribution lines of around 250-300 miles on average.
Farmers produce commodities, so are “price-takers” in economic lingo—this means they must accept whatever price the market will bear, so are subject to commodity price fluctuations. In the case of milk, the price fluctuations have been brutal.

TRADINGECONOMICS.COM HTTPS://TRADINGECONOMICS.COM/COMMODITY/MILK
A severe price drop in the late aughts and an extended period of low prices in the 20-teens (due, in part to the rapid growth of soy, almond, and other plant-based pseudo-milk) convinced the Barstows that they needed to change their strategy.
Rather than turning their land into a suburban bedroom community for Hartford, Connecticut or selling out to an industrial farming conglomerate, the Barstows decided to implement a circular economic strategy that continued their family’s historical continuity with the local community and made the entire area more self-sufficient.
The Barstows teamed up with several other family dairy farmers in the area to gain support from legislators and find investors interested in helping to fund the innovative transition they had in mind. With the groundwork laid, in 2013, the family installed a facility called an anaerobic digester that produces what is called “Renewable Natural Gas” or RNG.
RNG is produced when manure and other organic waste is dumped into an anaerobic digester and heated. The heating process accelerates the growth of microbes within the waste that breaks down the organic matter and releases methane. Methane—the prime component of natural gas—is burned as it comes out of the digester to generate electricity and waste heat, which is also recycled.
Denise explains that the digester—which she describes as an enormous mechanical stomach—produces enough electricity to power 1,600 homes and to offset the farm’s “carbon hoofprint” by 85%. The heat generated by the process is fed back into the digester to keep the process going and also provides hot water to eight houses on the farm, replacing heating oil or propane as a heating source.

Once the methane extraction process is finished, 98% of the organic matter is still left in the digester; this left-over liquidy-solid is termed “digestate.” The digestate is removed from the digester and used as a soil amendment for the farm’s forage crops. Denise says that using the digestate as a soil amendment has improved soil health, boosted crop yields, and allowed the farm to decrease its synthetic fertilizer usage by 90% (this is a big win from a climate change perspective because the main synthetic fertilizers, N(itrogen), P(hosphorous) and K (the Latin word for Potassium was Kalium) are produced using fossil fuels and / or transported long distances using fossil-fuel-powered ships or trains).
From a business perspective, the digester has allowed the Barstow Longview farm to remain a thriving business even though the dairy farming itself has struggled to break even for most of the last decade. The Barstow’s digester is built to accept food waste, so the farm makes money from “tipping fees” from local grocery stores and the Cabot Creamery to which it sells its milk.
Cabot, for its part, is an eager participant in the circular economy as well. Cabot buys up milk from surrounding dairy farms and pays tipping fees to return food waste to the Barstows’ and other anaerobic digesters. The tipping fees supplement the Barstows’ milk revenue and the RNG produced helps power the farms (which in turn cuts farm operating costs). In return, Cabot gets high-quality milk, saves something on landfill fees, and deepens its connection to local farmers.
In addition to the circular economic benefits, the production of the RNG makes the Barstow digester eligible to receive Renewable Energy Credits (RECs) which it can sell to utilities in the Northeast through its partner, Vanguard Renewables. (Vanguard manages the operations of the digester on behalf of the Barstows).
The digester offers the family an additional revenue stream to supplement the milk production and their other source of income—a farm store that the family opened back in 2008. The Barstow Farm Store sells fresh dairy, beef, and prepared food to local diners and to groups who come to the farm for by-appointment farm tours. In addition, the Farm composts manure from the heifer barn and sells that to local hobby farmers and suburban gardeners.
“Hold on a minute,” you’re probably saying. “How do dairy farmers have time to do all this extra work? Aren’t they up before the crack of dawn milking cows?”
As a matter of fact, since 2014, Barstow’s Longview Farm has been using robots to handle the milking. Cows are outfitted with what Denise calls a “Bovine Fitbit” that tracks the cows and allows them into a milking robot unit whenever the cow feels the need to give milk. Once the cow is in the milking area, the robotic milking arm positions itself underneath the udder and uses advanced computer vision technology to position the teat cups for milking (see the BBC clip below for a good explanation from a dairy farm in the UK).
The robots clean the teats, then milk the cows in a completely consistent way that fits with the cow’s own preference for milking timing. Denise tells me that the cows experience a much more comfortable, leisurely day than when they were all milked in batches. The lack of stress and the increased comfort have a practical economic benefit: the cows end up producing significantly more milk. “Before the robots, we were getting around seven gallons of milk per cow per day. Now, we get around 10 gallons per cow daily.”
The cows are happier and healthier, the work is done more efficiently, and the Barstows have more time to run the other parts of their business—truly, this is a winning solution all around.
What is an entrepreneur?
An entrepreneur is someone who sees a problem and designs a creative, cost-effective way to solve it. Denise and her family meet this definition to a “T,” investing in cutting edge technology, forming value-creative partnerships, and carefully considering how to not only survive but thrive in a difficult competitive environment.
What’s more, the Barstows are producing and marketing products that have true social value—nutritious milk, delicious ice cream and baked goods, and nutrient-rich compost to improve local soil health—especially compared with the social value destruction wrought by aforesaid man-children (FTX, “The Metaverse,” Free Speech Twitter).
Denise and her family knows, as I know, that we will need to start arranging our society in a very different way if we are to survive as a civilization over the next hundred years. Barstow’s Longview Farm is refocusing their community in Western Massachusetts around local food production and self-sufficiency. This is the way we will build a path to the future.
Intelligent Investors take note.