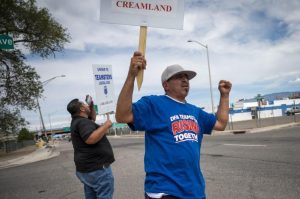
That means using the tools and skills available to them. The father and son are competent welders and Nick trained in boilermaking before returning to work full-time on the farm.
It means a lot of the work is done by themselves, and they employ a relief milker for three shifts a week.
They milk a 400-cow self-replacing Aussie Red herd, in a 50-bay rotary dairy they installed in 2003.
The recent installation of solar panels on the dairy is the latest innovation that enables them to make dairy farming as efficient as possible.
According to Dairy Australia, hot water, milk cooling and milk harvesting accounts for 80 per cent of energy use on a dairy farm.
Work undertaken by consultants RMCG for Dairy Australia demonstrated that in Gippsland, total energy costs per 100 cows ranges from $3800 to $8400, and averages $6100.
Hot water costs per 100 cows ranges from $660 to $2500, averaging $1580. Milk cooling costs per 100 cows ranges from $1080 to $2550, averaging $1510. Milk harvesting costs per 100 cows ranges from $690 to $1720, averaging $1200.
This breakdown has also been completed for other dairy regions, and is available on the Dairy Australia website.
In rotary and herringbone sheds in Gippsland, milk cooling is the highest energy use, followed by heating water and milk harvesting.
By switching to renewables and stored batteries, most farmers in Gippsland have typically saved $0 to $2000 per year in energy costs, with a few saving $2000 to $9000 annually.
Victorian, NSW and South Australian governments have energy grants available to assist dairy farmers change to renewable options.
There is information on Agriculture Victoria’s website about the free Tier One and Two on-farm energy assessments and on-farm energy grants — part of the government’s $30 million Agriculture Energy Investment Plan.
The energy assessment on the Leppin farm was completed last year and the solar panels and battery installed only a few weeks ago.
“We installed 96 panels on the roof of the dairy shed — the result of an energy assessment by a third party,” Nick said.
The panels were funded 50:50.
“It was laborious to do the paperwork to apply for the grant,” Nick said.
“I had to provide three quotes and two years of financial information. Then I followed up with them three times over six months, before I received confirmation we would get the funding.”
The solar power now runs the dairy and heats the hot water for washing.
“Heat recovery on the chiller feeds the hot water service with 43°C hot water; that alone reduces a lot of our energy use,” Nick said.
“When the power is not being used during the day, we get about $0.10/kW back into the grid.”
Solar power also keeps the two milk vats cool.
Toby and Nick have two milk vats, and it’s a strategy that has helped them at times. Particularly because of their steep terrain, if weather prevents or holds up the truck from collecting milk, then extra milk can be pumped into the second vat.
Nick said it also means they can keep milking, if the truck arrives to collect during milking.
“And if you have a cow who’s on antibiotics and you mistakenly collect her milk, you don’t have to stop milking; you just switch over to the other vat,” he said.
Having two vats is also an excellent way to identify problems with cooling the milk.
“If one vat is failing, for example, the thermometer is high on one vat, you know there’s something wrong with that vat,” Nick said.
“If the thermometer on both vats is high, you know there’s something wrong with the milk plant.”
One of the challenges they manage is the steep hilly terrain of their farm at Bena.
As much as possible, systems are automated, or constructed for application to be as simple as possible.
Auto-gates are used throughout the property, a simple set-up with a release timer connected to a double-handed bungee.
“I set it with morning and afternoon times over several days, using my phone,” Nick said.
“No-one has to go to the paddock to let the cows out. It saves us time and keeps machinery use on the laneways and paddocks to a minimum.”
The auto-gates are used on paddocks, laneways and the feedpad.
At strategic times of the year, when drying off cows and in winter, they use a concrete feedpad with a hayfeeder to feed the herd.
Using the hayfeeder on the feedpad is the most effective way of ensuring all fodder is eaten by the herd during winter and wet periods. It also means traffic is reduced in laneways and paddocks at a time when the farm is wet.
The concrete pad was installed in 2005, next to the dairy.
Recently, Toby and Nick purchased a second hayfeeder, to replace the original. The hayfeeder enables at least 110 cows to be fed from each side of the feedpad.
The cows’ heat detection collars simplify insemination procedure. Two base stations at the dairy use wireless connection to identify cows potentially ready to join.
“Using two base stations to scan the cows means the system is not overloaded with data,” Nick said.
The cows identified with a heat spike at milking are auto-drafted into a set of yards on the dairy pad.
Nick or Toby can then double-check the temperature pattern of each cow against years of data, decide if she is likely on-heat and administer AI.