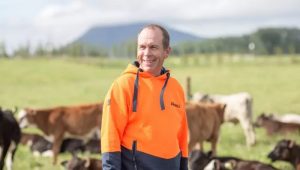
And Teagasc research officer Dr John Upton says that by making other slight changes inside the farm gate, farmers can make additional savings on their energy costs.
Dr Upton told farmers at the Energy in Agriculture conference in Gurteen College, Co Tipperary that 42 kilo-watts of electricity are consumed for every tonne of milk produced and that milk cooling is the largest consumer of energy, followed by water heating, milking and the milking machine.
He added that there can be a huge difference in annual energy bills on two farms that have the same number of cows.
“The range in energy bills is enormous, from €2.50 to €9 per tonne of milk sold. There’s no one reason why a farm is efficient or isn’t efficient, we have to tackle all these areas. It’s not efficient to just to look at one area,” says Dr Upton.
Night rate
Dr Upton advises that every dairy farmer should switch to night-rate electricity as it can save the average 100-cow farm in the region of €1,000 per year on their energy bills. “The day rate is 18c and the night rate is 8.5c per kilo-watt hour. There’s a small increase in the standing charge but it’s very small in the scheme of things,” says Dr Upton. “The night rate hours are 12 midnight to 9am, which changes to 11pm to 8am in the winter.” He says farmers can also save hundreds of euro on their energy bill each year by switching providers.
Milk cooling
The best way to save energy on milk cooling is to install a pre-cooler with Dr Upton insisting that payback on this investment will be less than five years.
“The goal of pre-cooling is to cool the milk within five degrees of incoming water temperature. If your well water is at 10 degrees you want to be pre-cooling the milk at 15 degrees before it goes in to the bulk tank,” he explains.
“This removes half of the energy from the milk before you ever have to refrigerate it.
“To achieve this goal you need to get a milk to water ratio of one is to two – for every litre of milk that goes through the plate cooler you want to put through two litres of water.”
Variable Speed Drive
Dr Upton says installing a Variable Speed Drive is paramount to achieving energy-efficient milk cooling as they speed up and slow down according to how much milk is going through the receiver jar of the milking machine.
“In addition to that you need adequate water pipe sizes – you need a connection from the well to the plate cooler that is at least an inch in diameter to deliver the correct water flow.
“Then you can use a solanoid valve on the pipe to help reduce water wastage.
“It opens when the milk pump is operating and closes when it’s not.
“This is the best investment you can make.”
Milk vacuum pump
Dr Upton explains that the best way to reduce energy consumption of the milking machine is by using variable speed control on the vacuum pump, which will reduce its running costs by about 60pc.
“The way that works is the regulator of the vacuum pump system is replaced by a sensor that’s connected up to a piece of technology called an inverter which changes the speed of the vacuum pump motors,” he says.
“When we apply clusters to cows in the pit, the vacuum pump will speed up; when we’re not doing anything in the pit, the vacuum pump will be running at a slow speed.”
Water Heating
Electrical water heating is the most common technology that is used on farms and it’s perfectly adequate for 80-90 cows herds as it’s a very good blend between capital costs and money costs, according to Dr Upton.
However, he adds that for larger farms it would be more cost effective to consider oil or gas systems.
“Under the day rate of electricity, it would cost you about €2 to heat 100 litres of water up to 80 degrees; at night rate that’s going to drop to €1,” he says.
“If you’ve got a gas system that will be about 90c and oil boiler around 65-70c depending on price of oil.”
Heat recovery unit
The number one way to reduce the running costs of the water heating system is to install a heat recovery unit.
“A heat recovery system captures waste heat and stores that heat in a tank of water,” says Dr Upton.
“Heat recovery can reduce water heating costs by 40-50pc. If plate cooling is installed, the savings would be 25pc.
“The thing to watch about heat recovery is that the payback will vary a lot depending on how much hot water is being used, they tend to pay for themselves more quickly on larger farms and it’s important to check the payback on this on a case-by-case basis.”
Lighting
Good design and making use of natural light can save farmers money on their running and service costs.
Dr Upton advises that light fixtures should be suspended just over the milking pit and that lights should be placed where they’re needed rather than from a height.
“Specific tasks require different levels of lighting. Tasks like milking, office work and cleaning the bulk tank room require high levels of lighting – upwards of 500 watts – whereas for general area lighting of corridors and so on, 200 watts is more than adequate.
“LED tubes are by far the most efficient. They should be robust and last a long time.
“Light fittings should be splash-proof or water-proof depending on the area they are installed in.
“Another key point to do with lighting on dairy farms is they shouldn’t cause interference with other areas of the farm such as automated heat systems.”