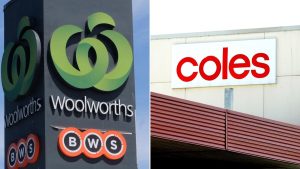
Jana Hocken, who worked as an engineer with Toyota and a lean management consultant across the globe, was horrified by what she saw on farm when she and her husband took on the management of his family’s 1000-cow operation.
But she realised the same lean management principles she had helped introduce to large businesses could be applied successfully on farms.
“One of the definitions of lean is the relentless pursuit of identifying and eliminating waste in all forms in order to improve business performance and customer satisfaction,” she said.
“If we look at our processes in the eyes of customers … and we define value in the eyes of our customer, then 95 per cent and sometimes more of our processes are non valued-added in the eyes of customers.”
But this created the opportunity.
These processes could be simplified or reduced without having any impact on the customer.
This would not change the milk price or government regulation or any of the other external pressures on the business, but it would help people working in the business do things in a better way.
It would mean fewer resources and less time was needed to do things.
Ms Hocken said waste in a lean management fell into eight categories, that could be represented by the acronym DOWNTIME:
Defect – when things go wrong, fix a fence, milk goes down the drain, cows in the wrong paddock.
Overproduction – for example, stock, feed, so using resources for something not needed.
Waiting – for animals, decisions, supplies.
Not-Utilised people – particularly not listening to people’s ideas that could make processes better.
Transportation – moving stuff around unnecessarily, such as moving a pile of feed or mineral from one place to another.
Inventory – having more of what is needed, for example buying medications that were not needed that expire.
Motion – people moving around when not needed.
Extra processing – doing more than is required to get an outcome.
Ms Hocken said it was vital to establish clear, standardised processes for tasks done on the farm.
The keys were to provide specific directions, use visualisation where possible and ensure people understood the end outcome.
It was also important to create open, transparent workplaces where teams were engaged and empowered and there was two-way discussion, where people could ask questions and receive feedback.
Ms Hocken provided an idea of what this waste could look like on a dairy farm (see Figure 1).
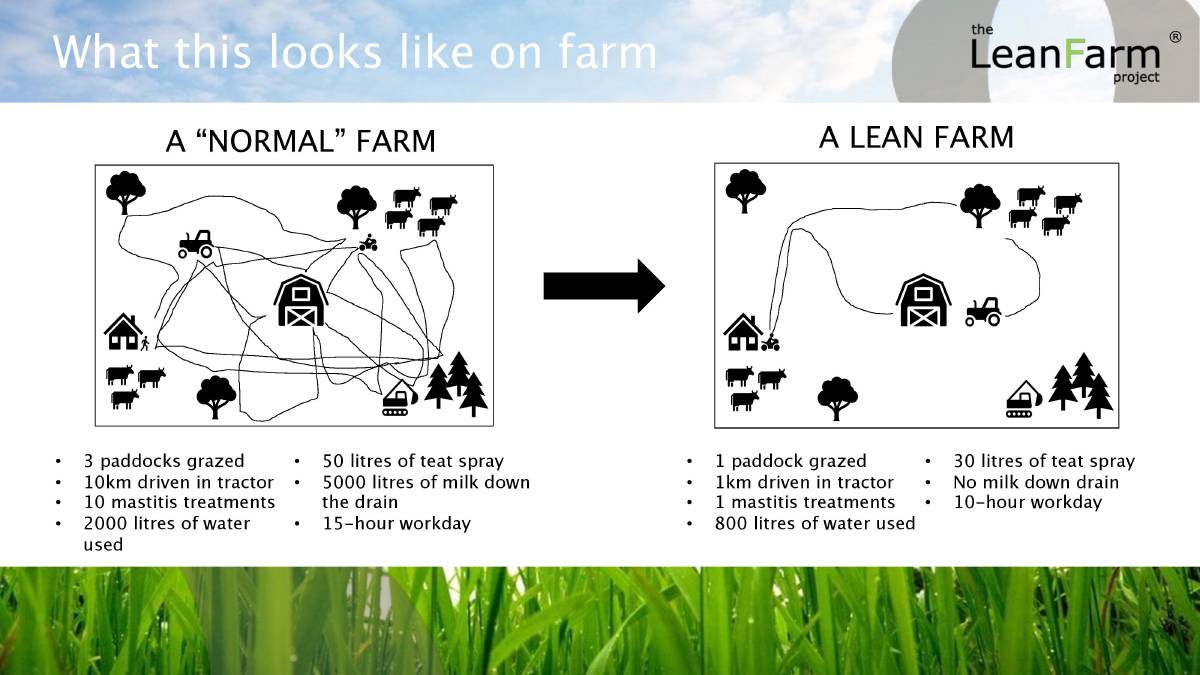
Simplifying processes and setting up the farm in a more logical way could reduce waste in many areas: pasture, feed, effluent, labour, resources used and time.
She gave a specific example of a change implemented on their farm in Teat Seal treatment (see Figure 2).
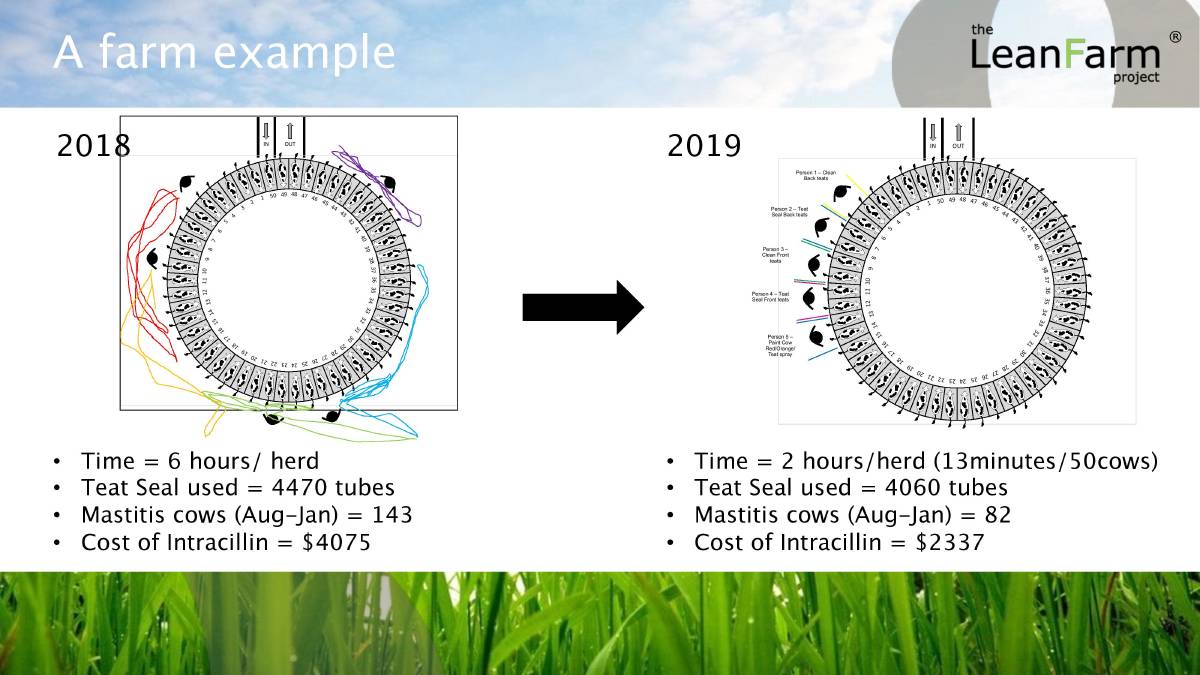
Under the old system, five staff members did full treatment on individual cows on particular parts of the stationary rotary platform.
Under the lean system, the process was turned into something like an assembly line. The rotary moved at a 20-second intervals and each person was allocated a specific task to do on every cow and the five staff members stood side by side around the platform. One person cleaned the back teats, the next person sealed the back teats, the next person cleaned the front teats, the next person sealed the front teats, and the last person painted the cow red/orange and teat sprayed.
The change cut the time spent from six hours to two hours, reduced the number of Teat Seal tubes used, and reduced the subsequent number of cows with mastitis, halving the cost of antibiotic used on the farm.
“All we did was change the process, some impressive results just by thinking differently about how you do things,” Ms Hocken said.
The change produced a 66pc reduction in time, a 9pc reduction in Teat Seal, a 43pc reduction in mastitis and a 26pc reduction in costs. It also reduced the stress on the animal and the people, which also reduced the amount of effluent and the water needed to clean it up.
“If you do right things the right way, you’ll get right results,” Ms Hocken said. Looking after the environment, animals and land was good for business, it made business sense.
Ms Hocken has written a book, The Lean Dairy Farm, on how she applied these principles on a dairy farm.